The lack of stability in the convertible Z chassis is something that has frustrated Justin and I for a while. Over the years we had talked through different possible solutions to the issue and spent a decent amount of time looking over what other OEM manufactures had done to solve this issue and some aftermarket companies’ solutions. Also, both of our thinking has changed in terms of the importance that chassis structure and rigidity actually make. For a long time, the formula was more power = more better, after getting to spend time wrenching on and driving exotics that has changed. The underside of the Z doesn’t really have anything great for possible attachment points of a brace, so we decided to reinforce the frame rails to help add support and provide anchoring points for phase 2 of the project. We had these pieces custom stamped and then trimmed them to fit the profile of the OEM frame rails.
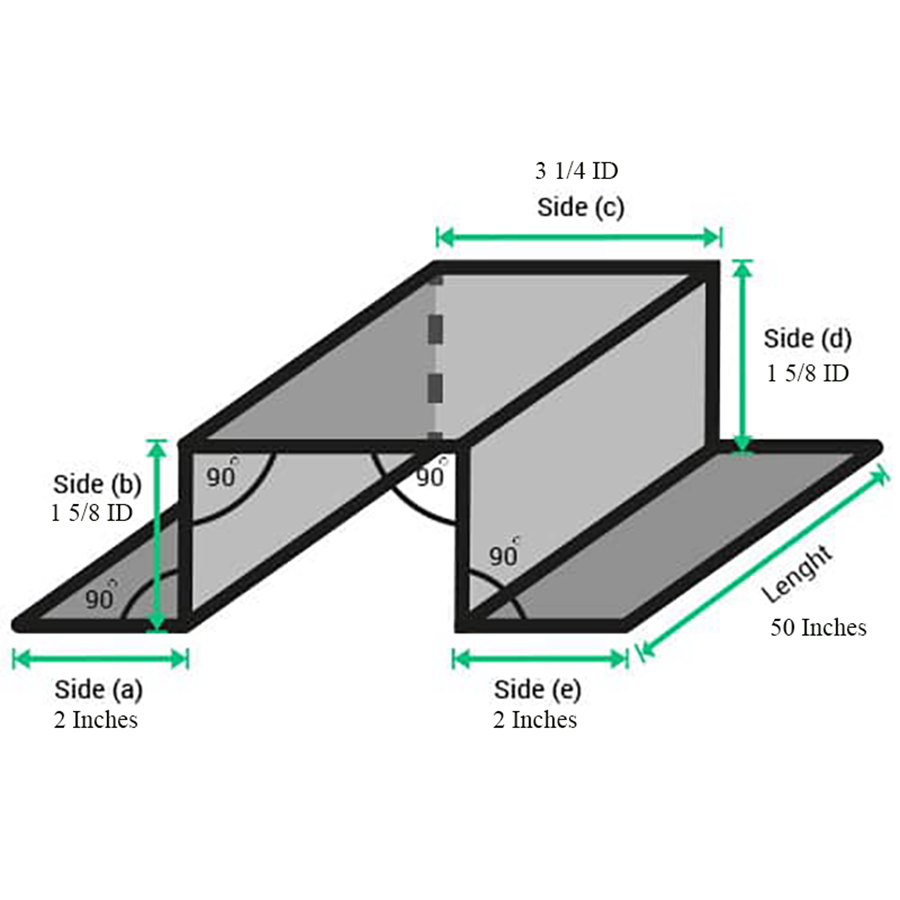
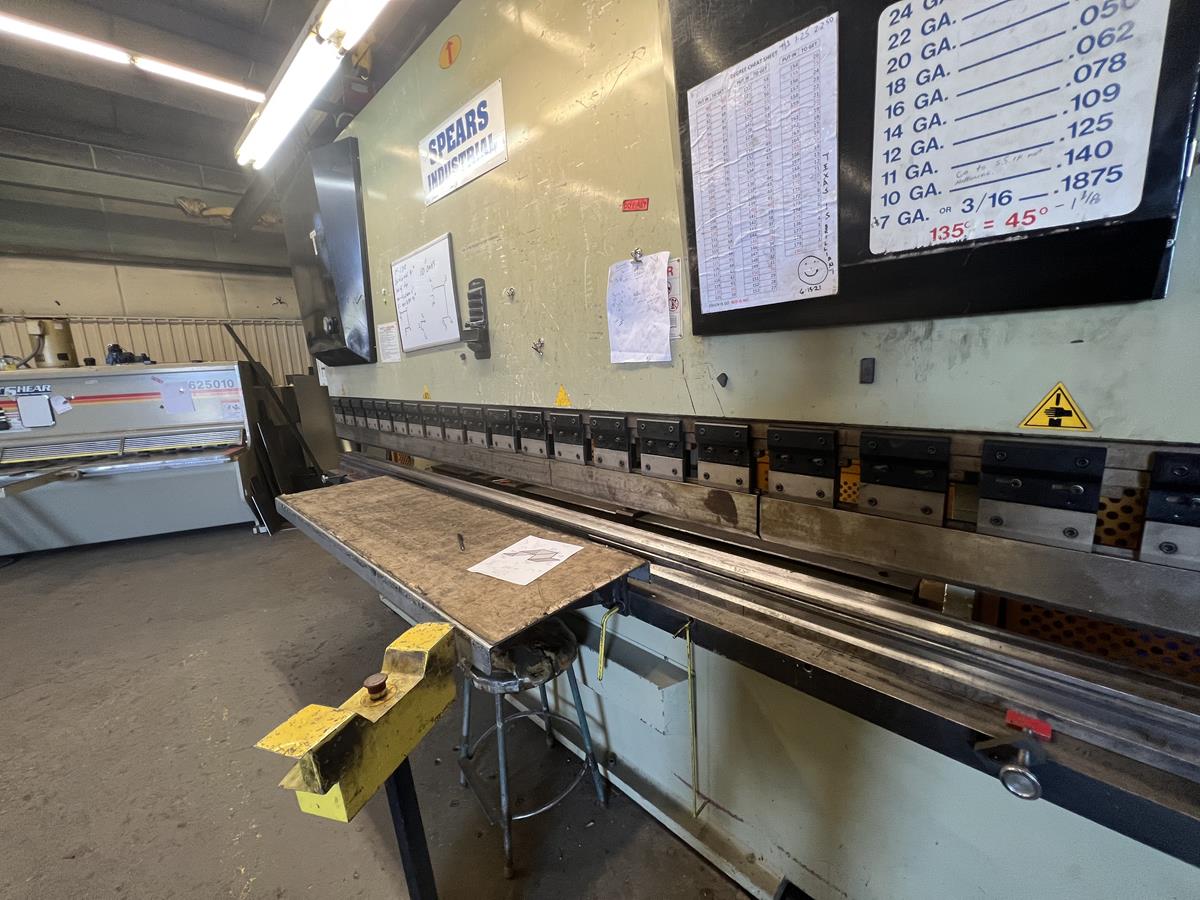
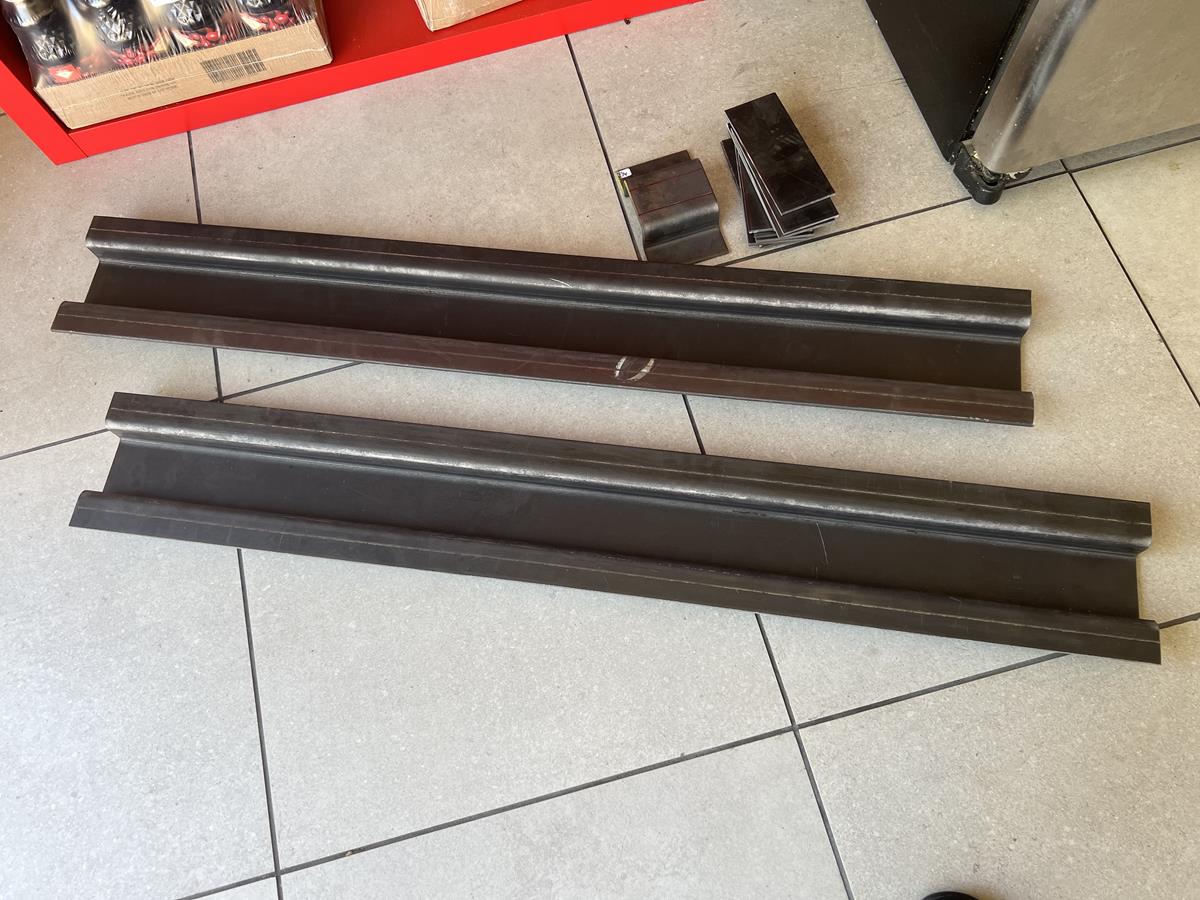
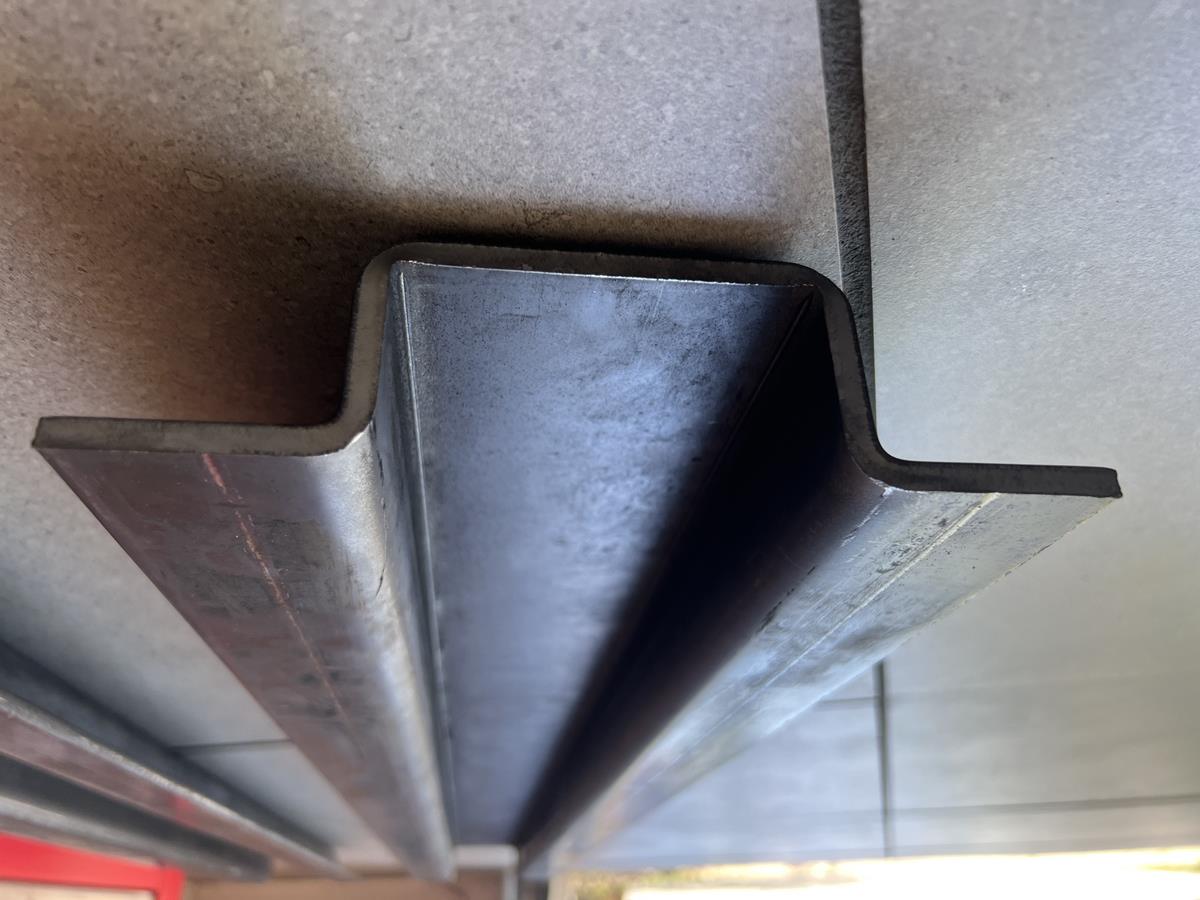
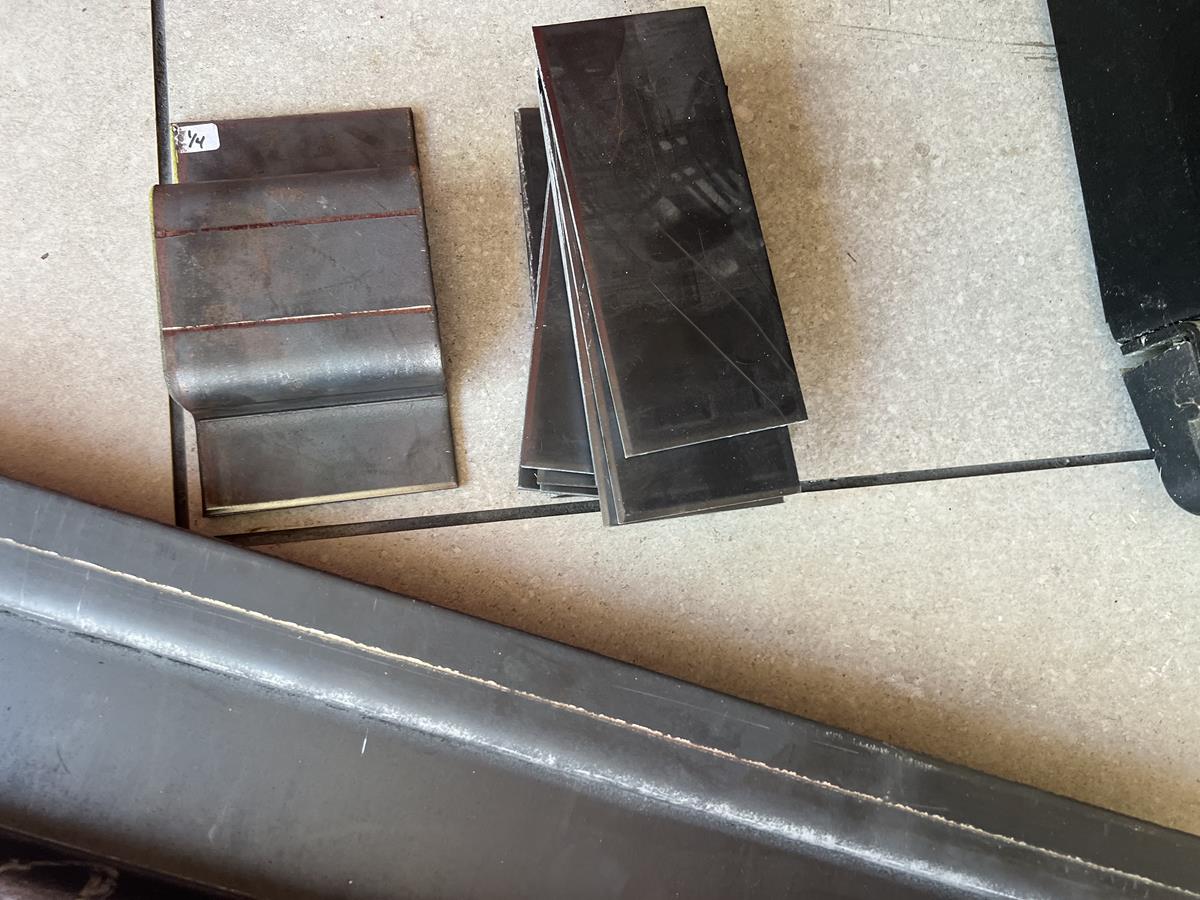
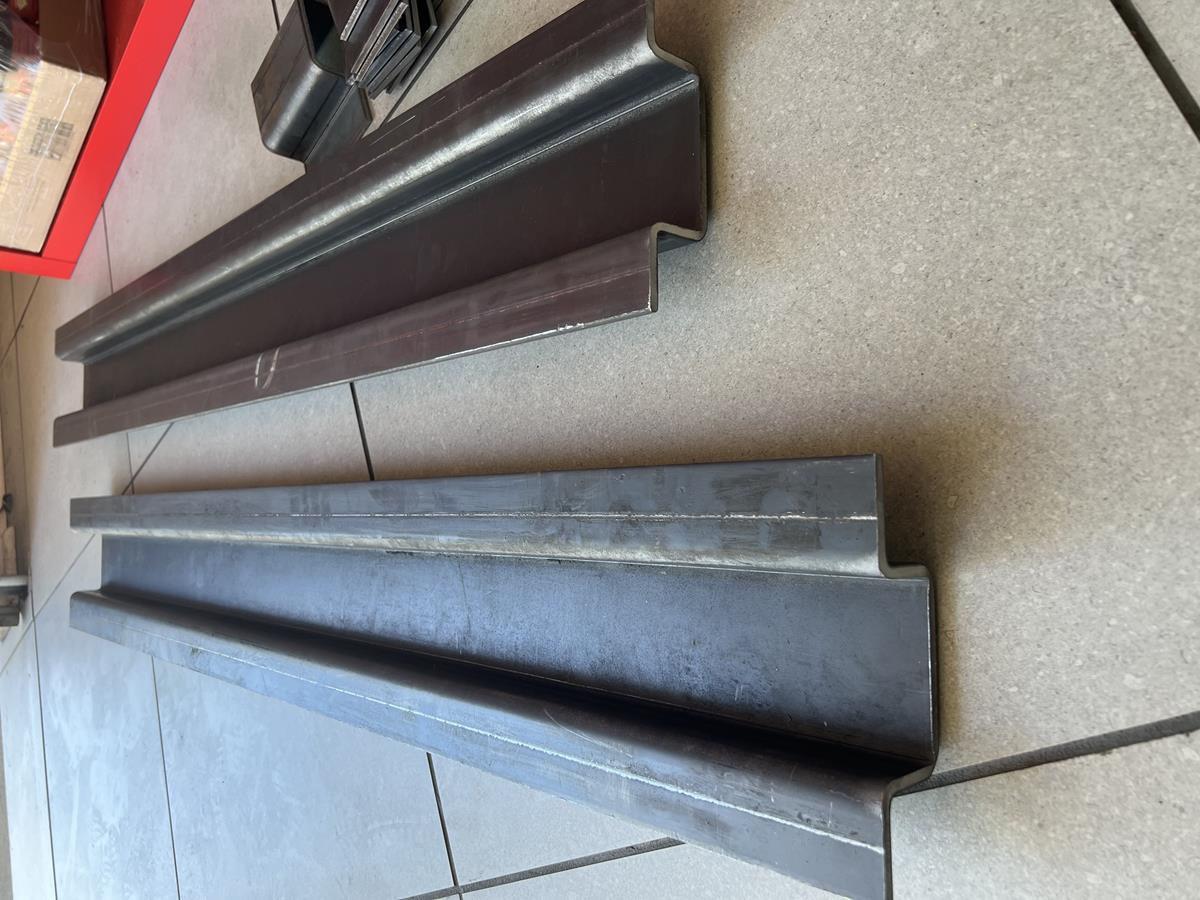
We had these top hats made in order to provide a way to secure the frame rail brace to the car 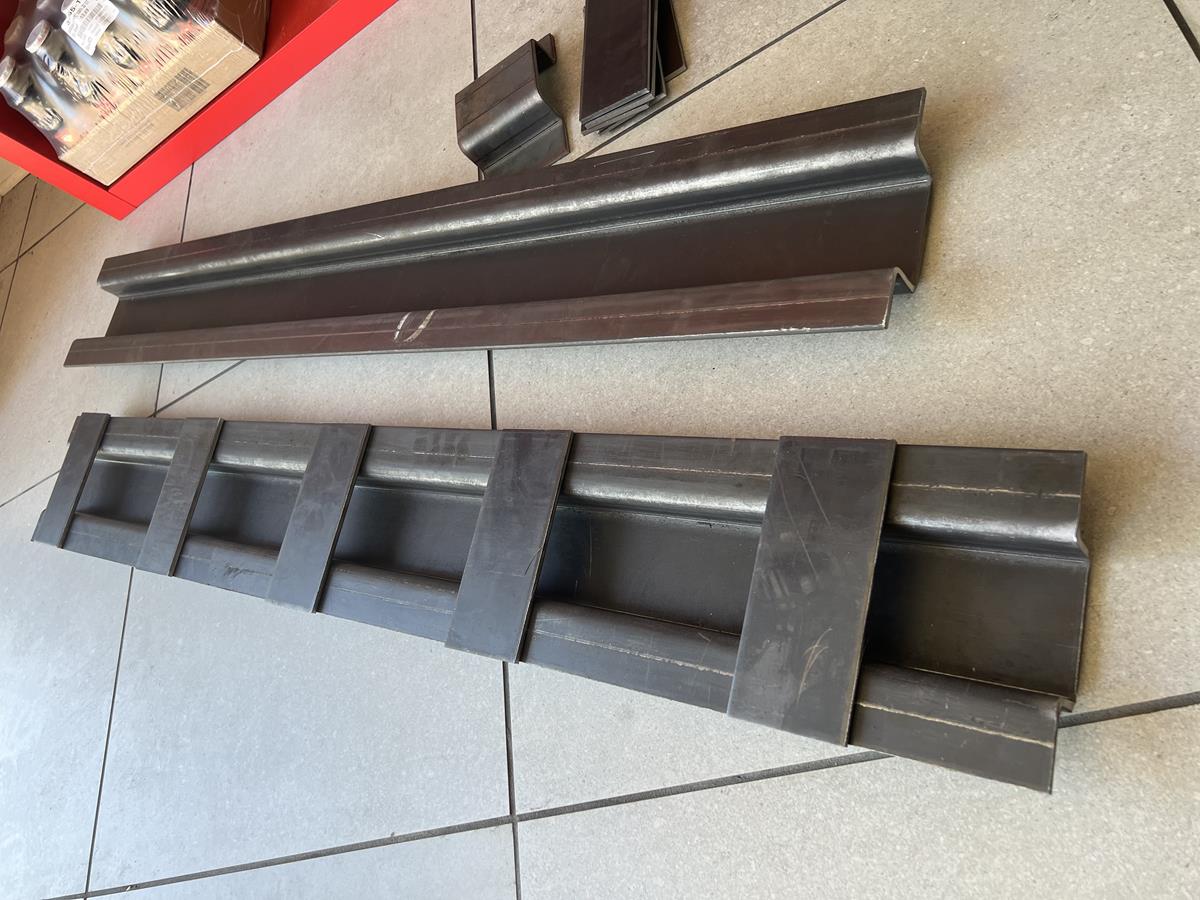
From there it was a lot of on / off for custom tailoring 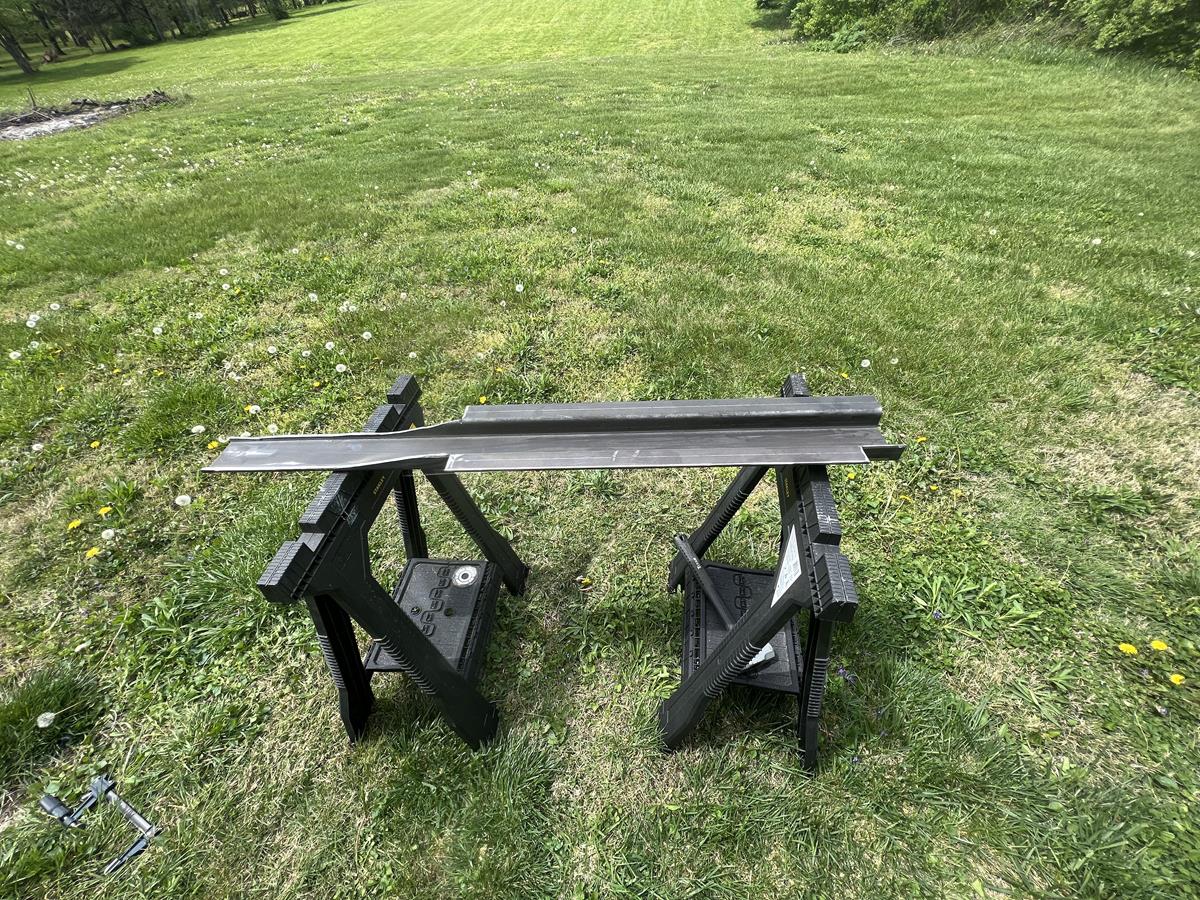
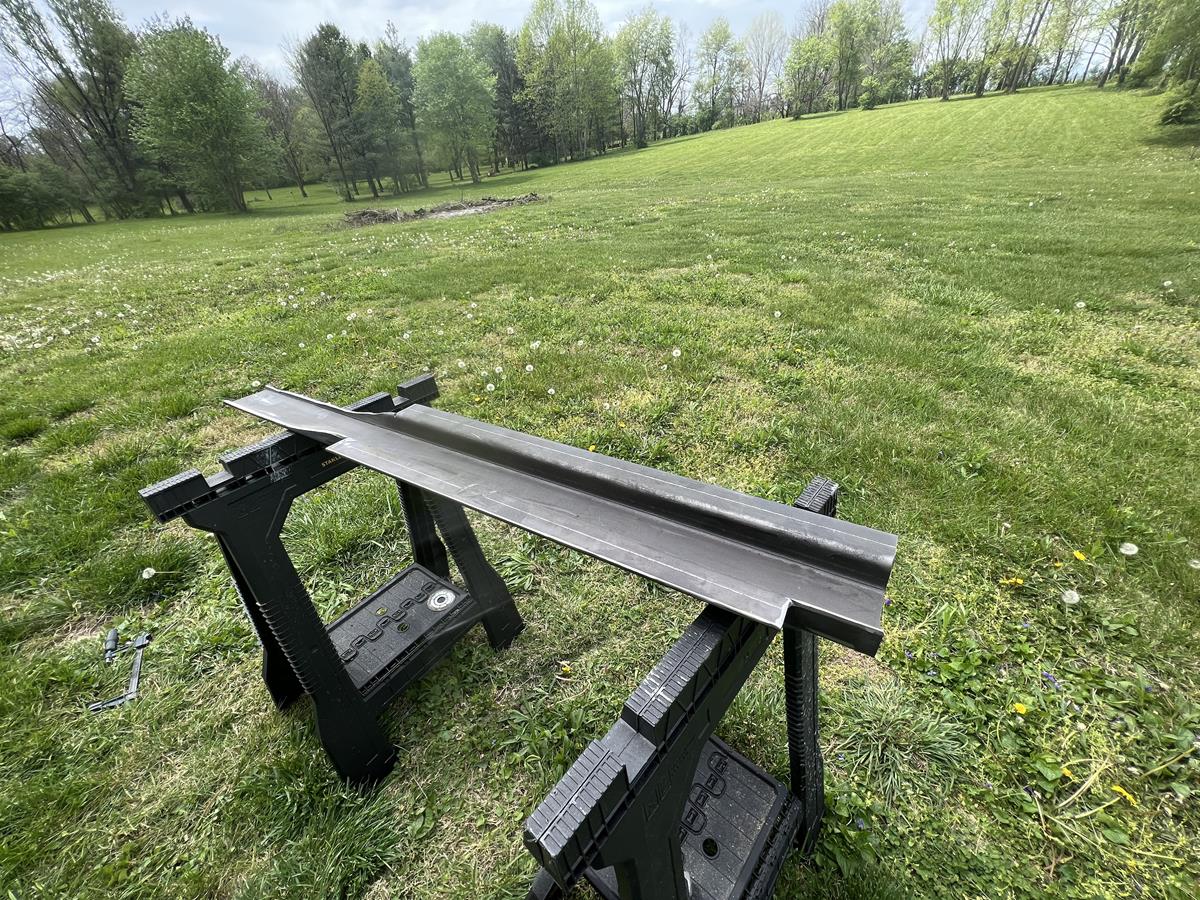
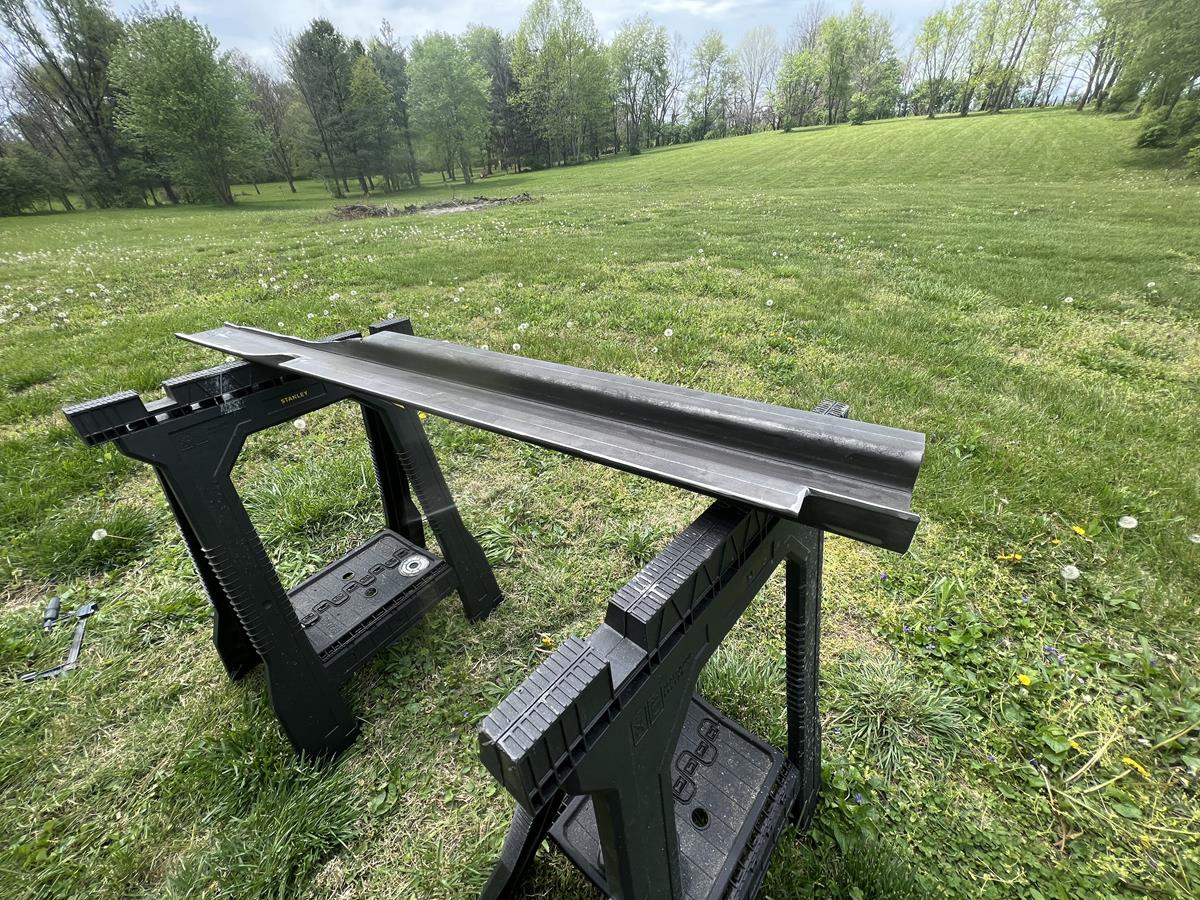
Mock Up placement of the top hats 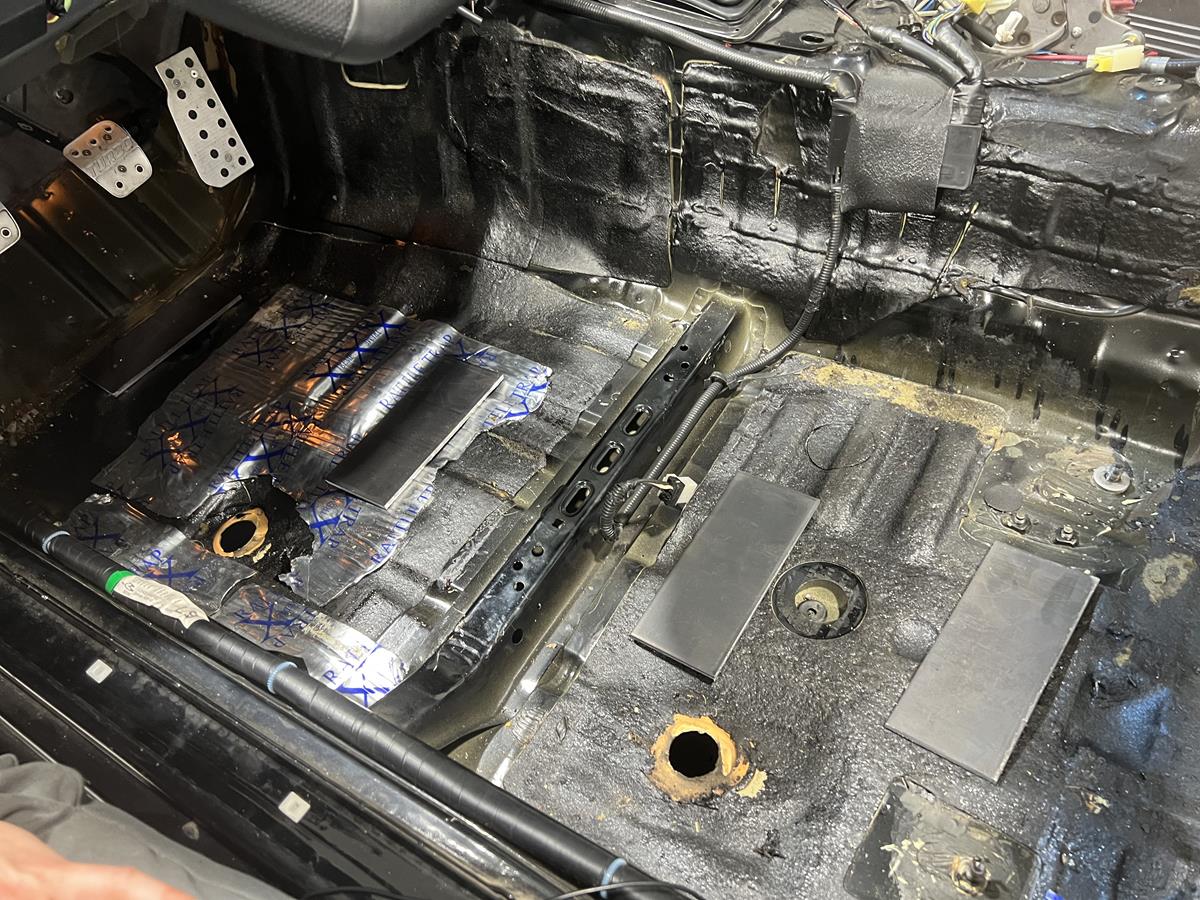
top hats drilled and ready 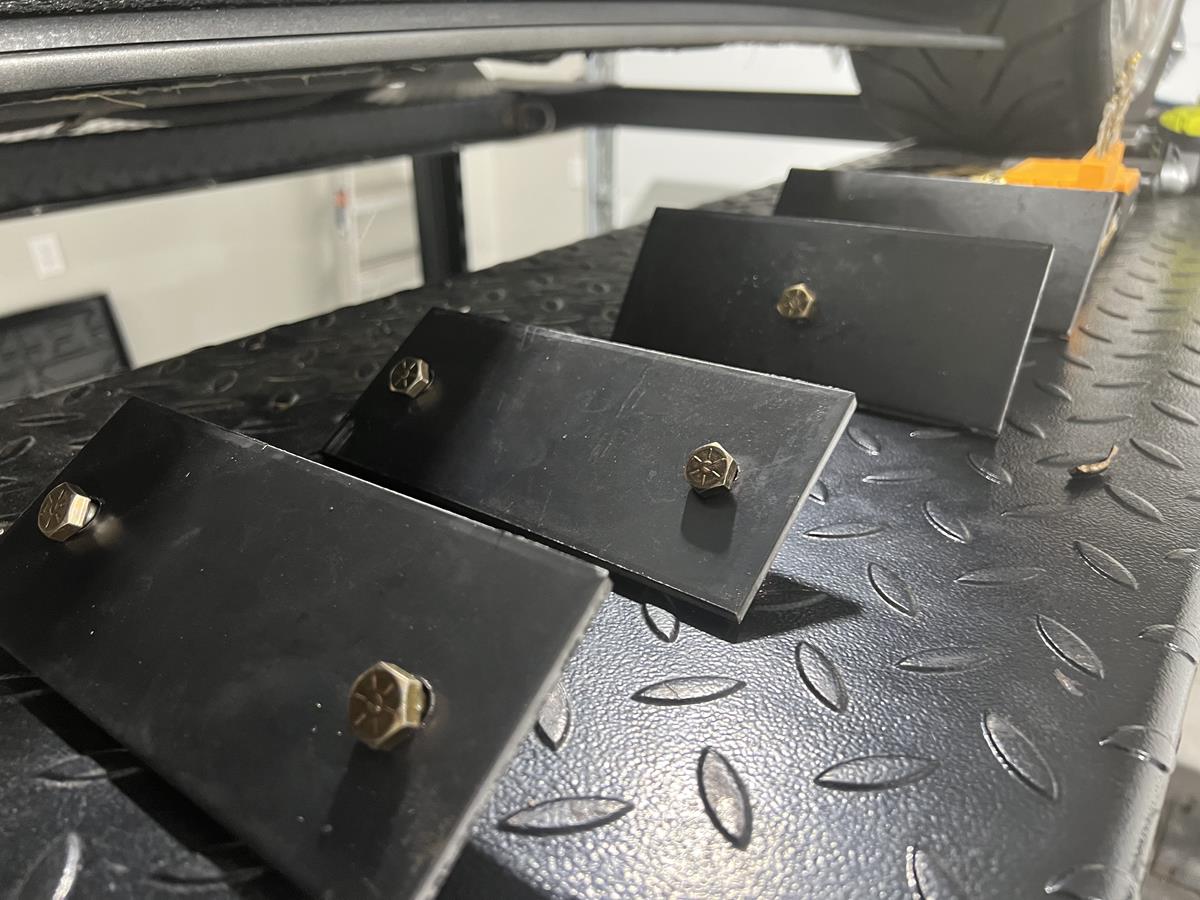
Everything in... 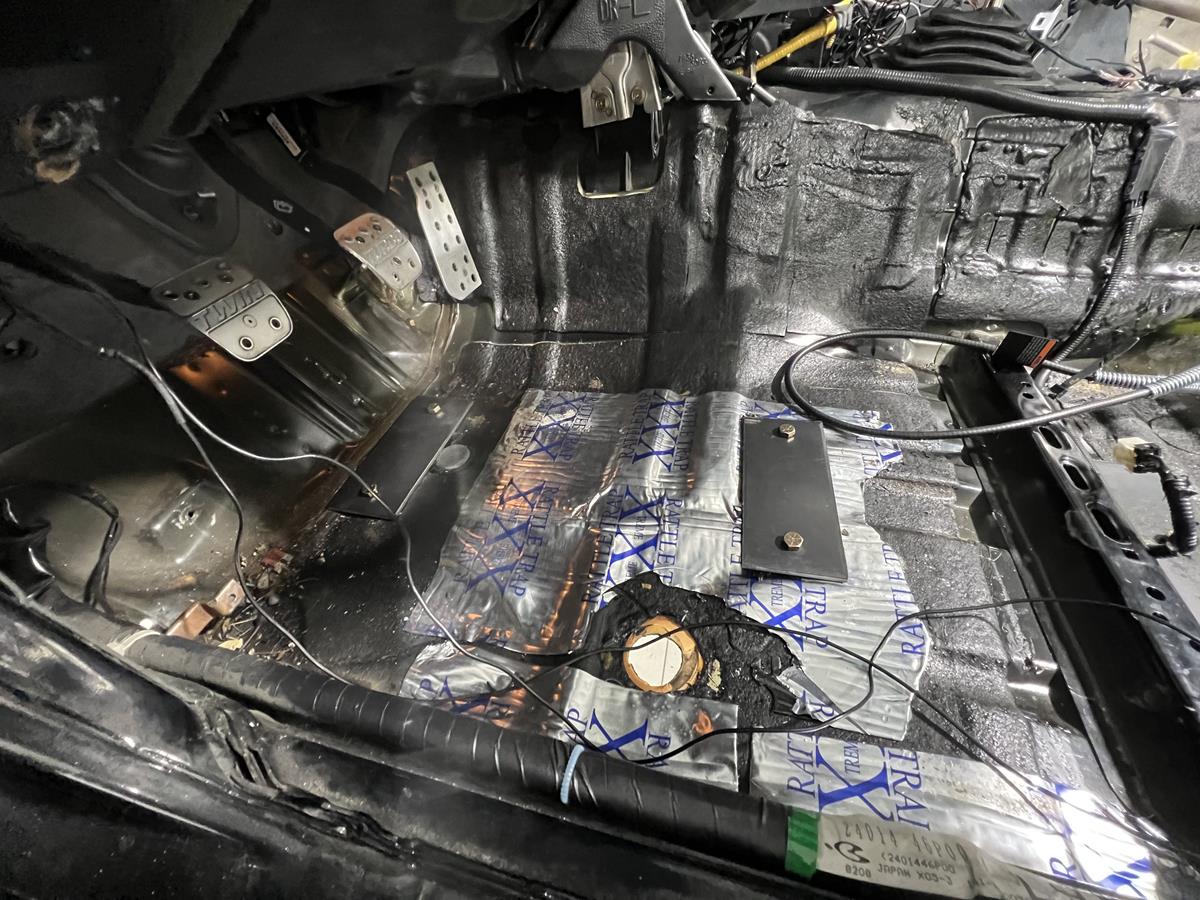
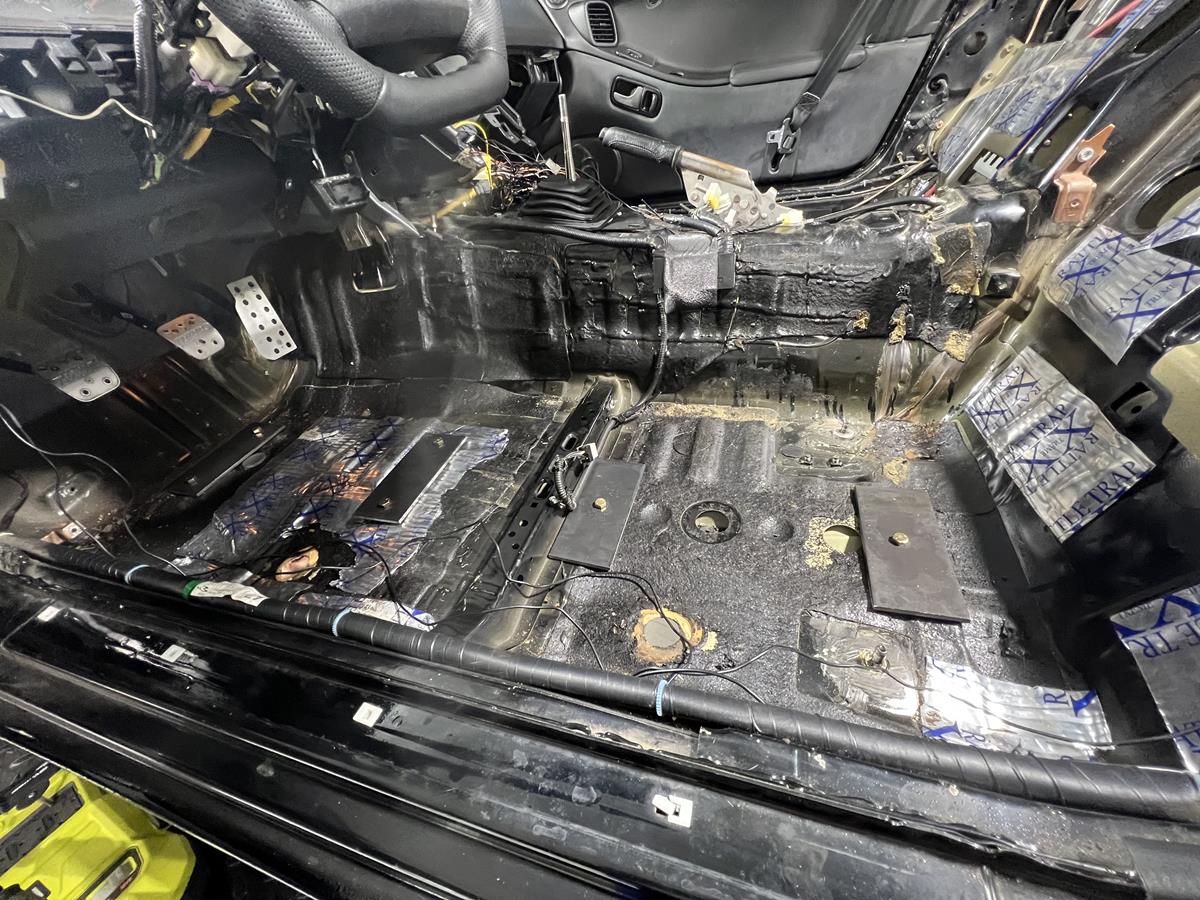
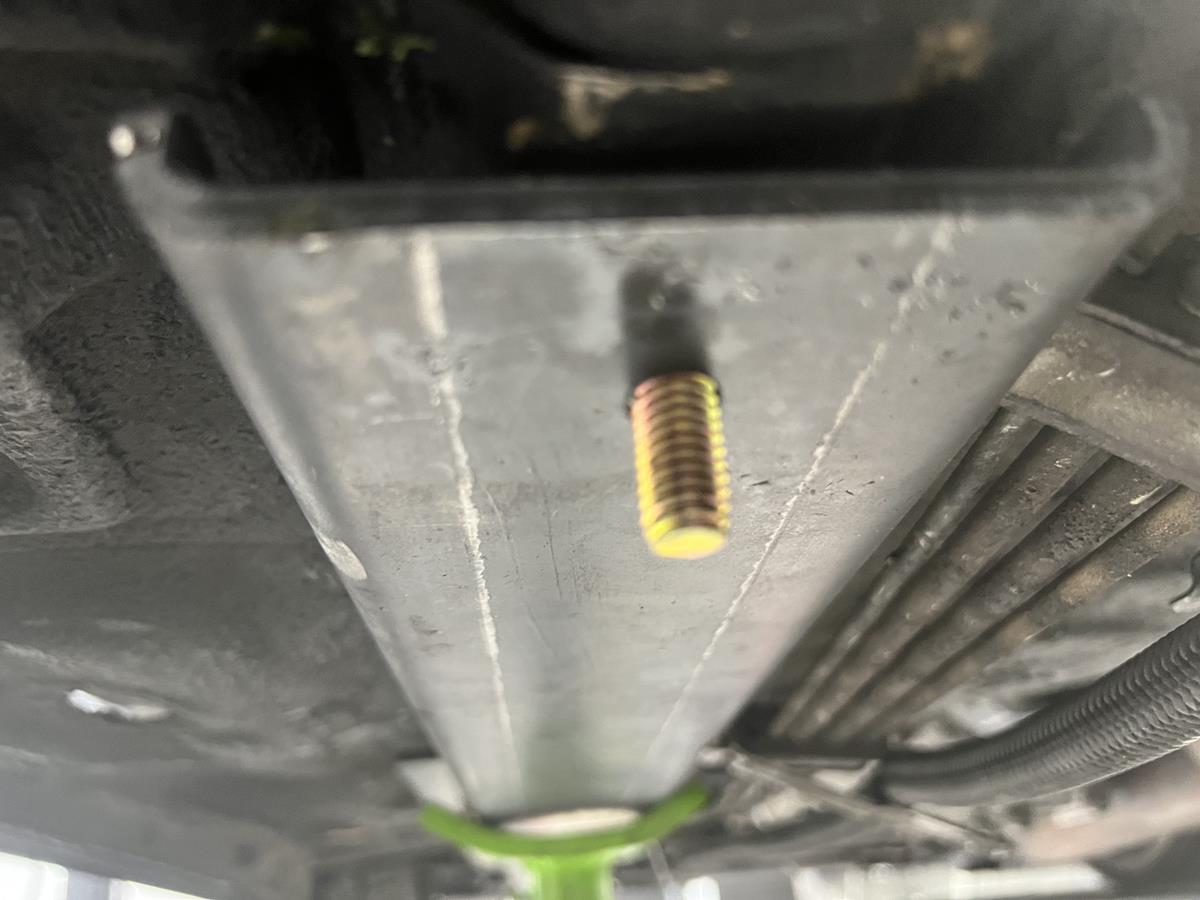
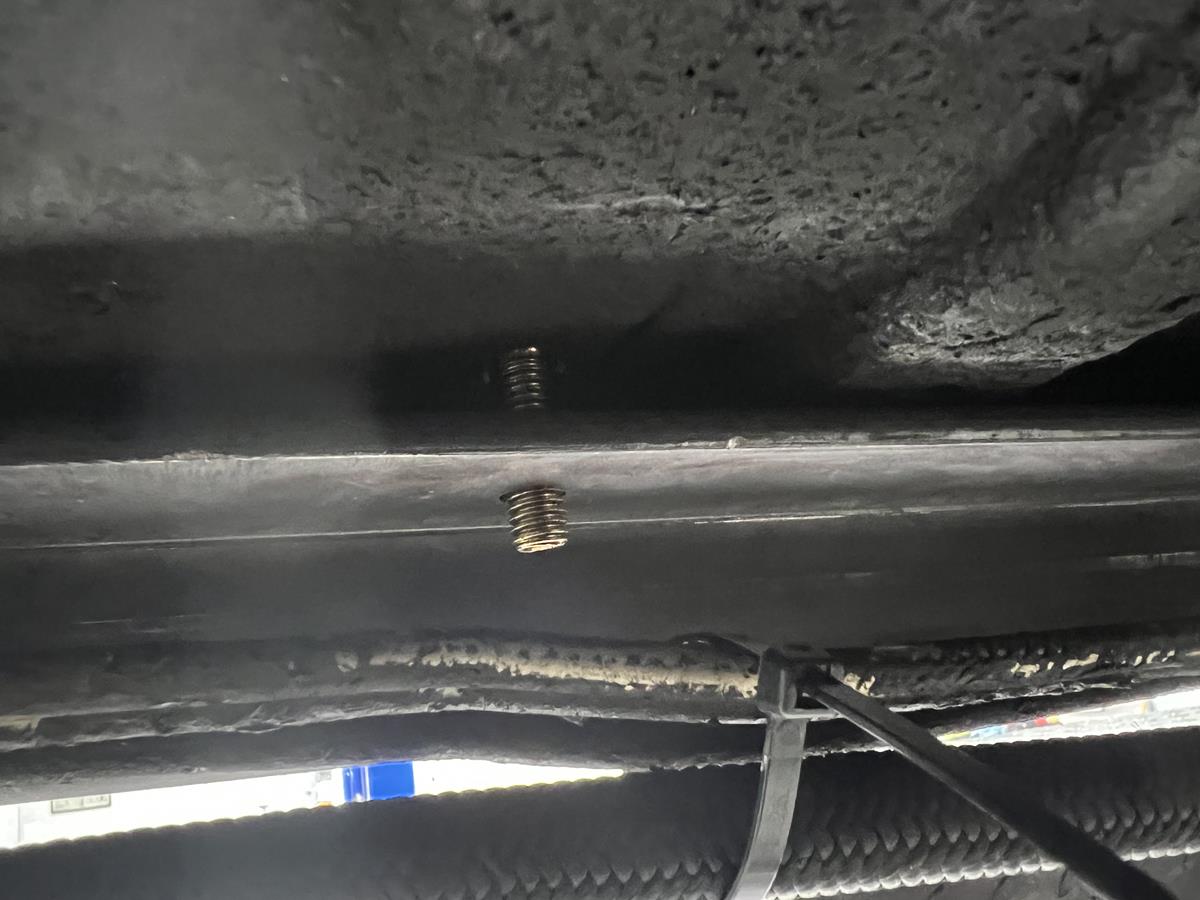
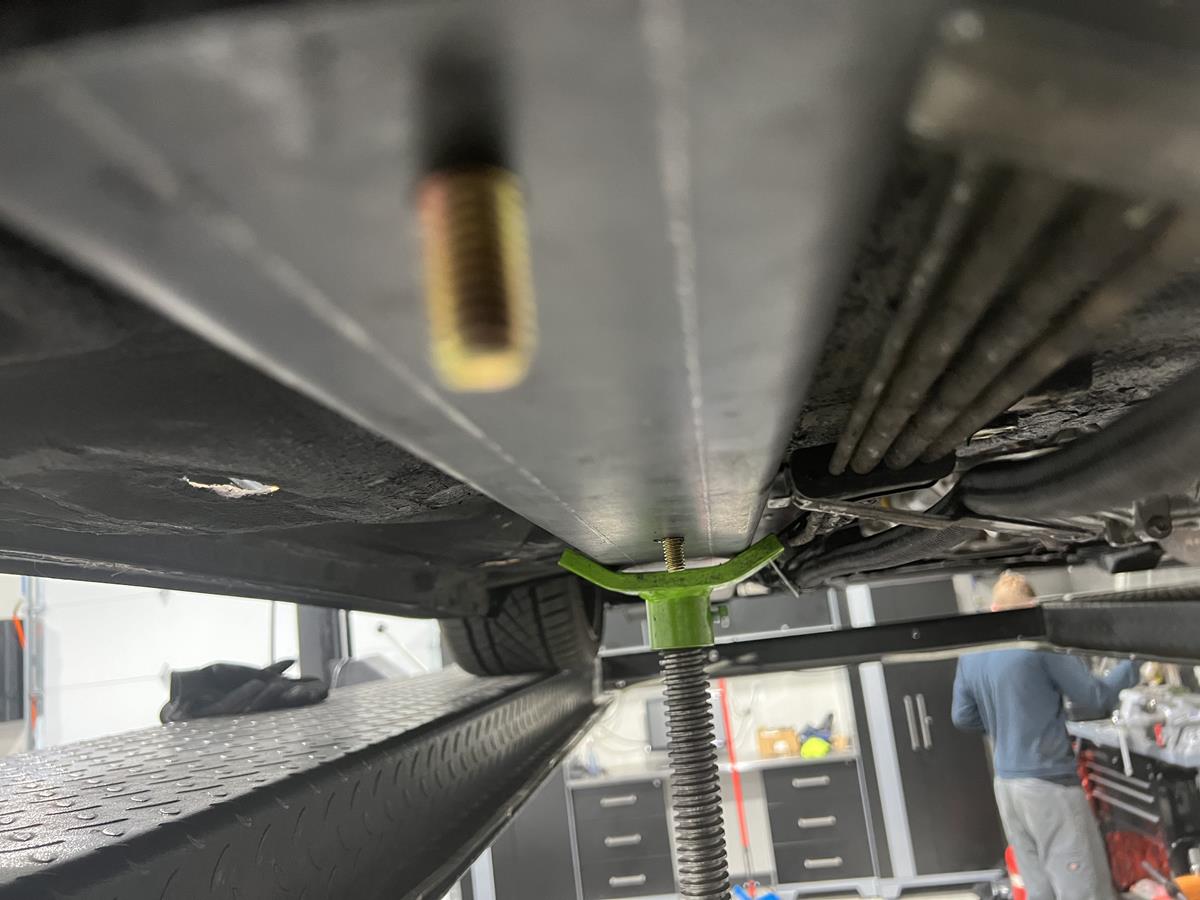
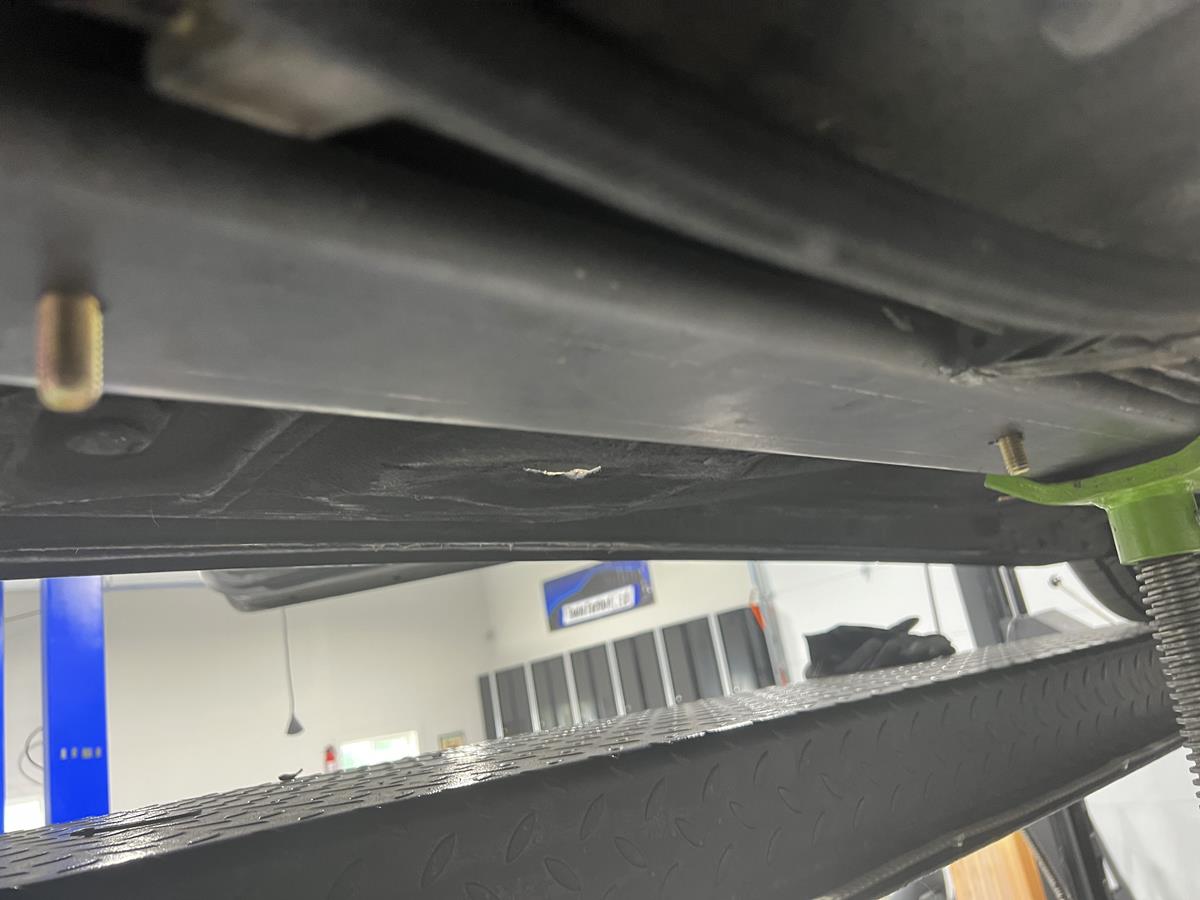
And the frame rail supports fully in. This alone added a noticeable difference in stability while driving. 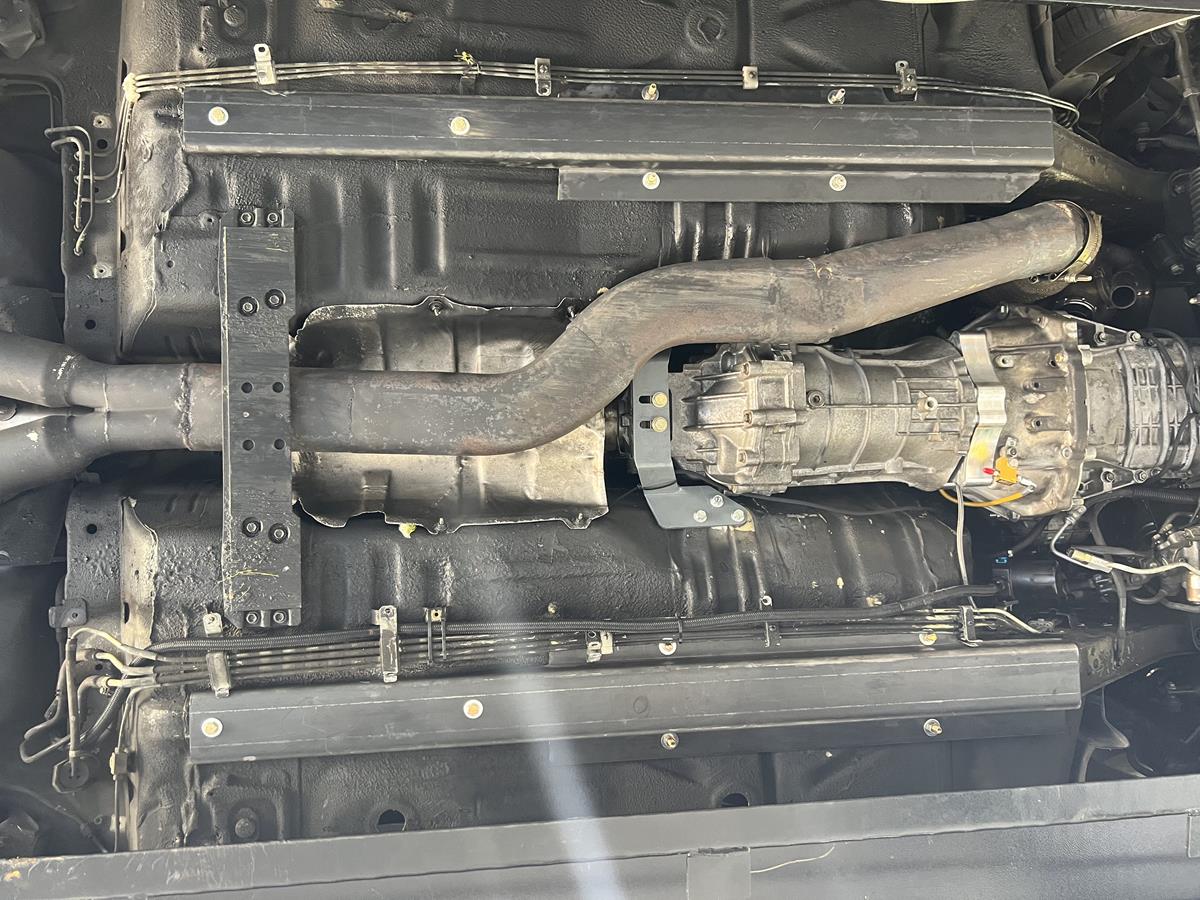
Next, we started to jack up different points of the car to see where we got the most movement and used tape to help get a better visual representation.
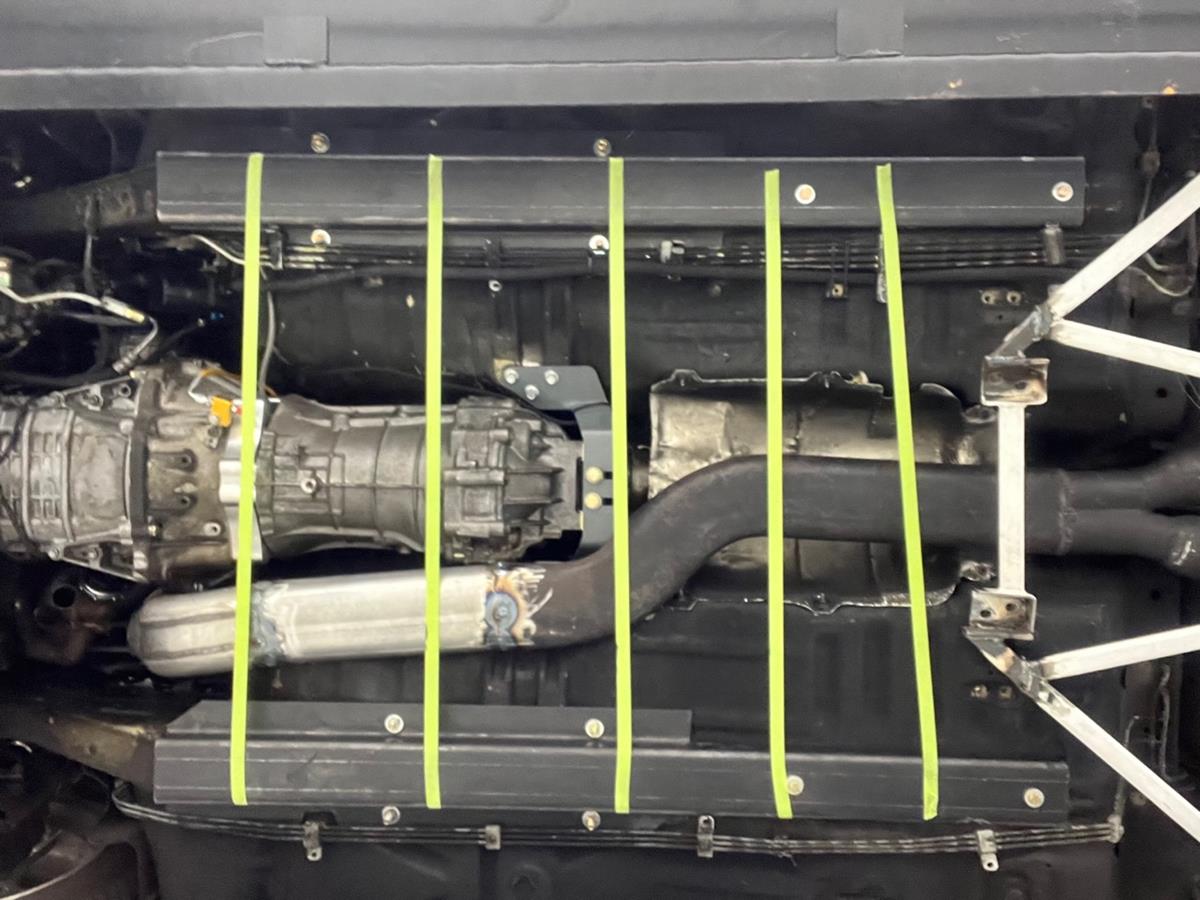
From here we started to mock up what a brace could look like. 
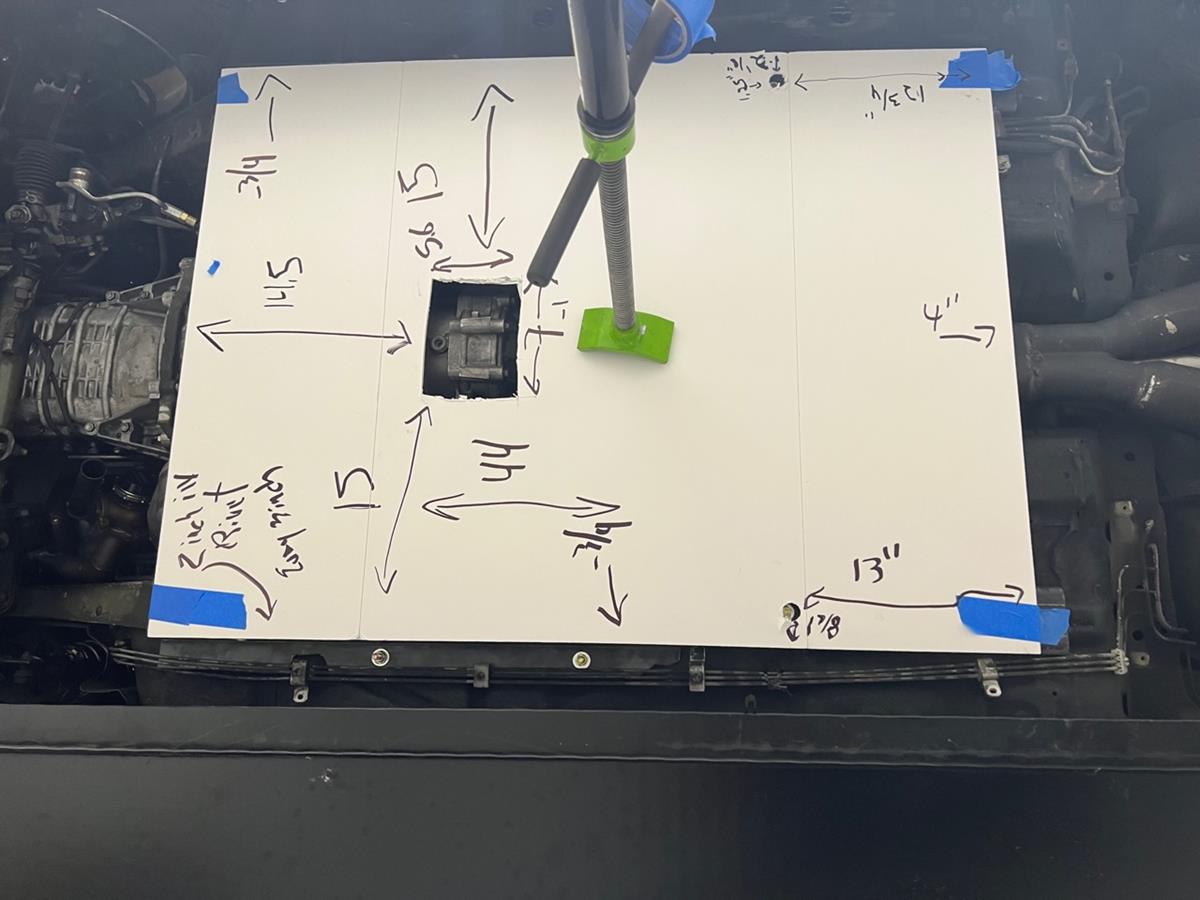
CAD Rendering of the brace
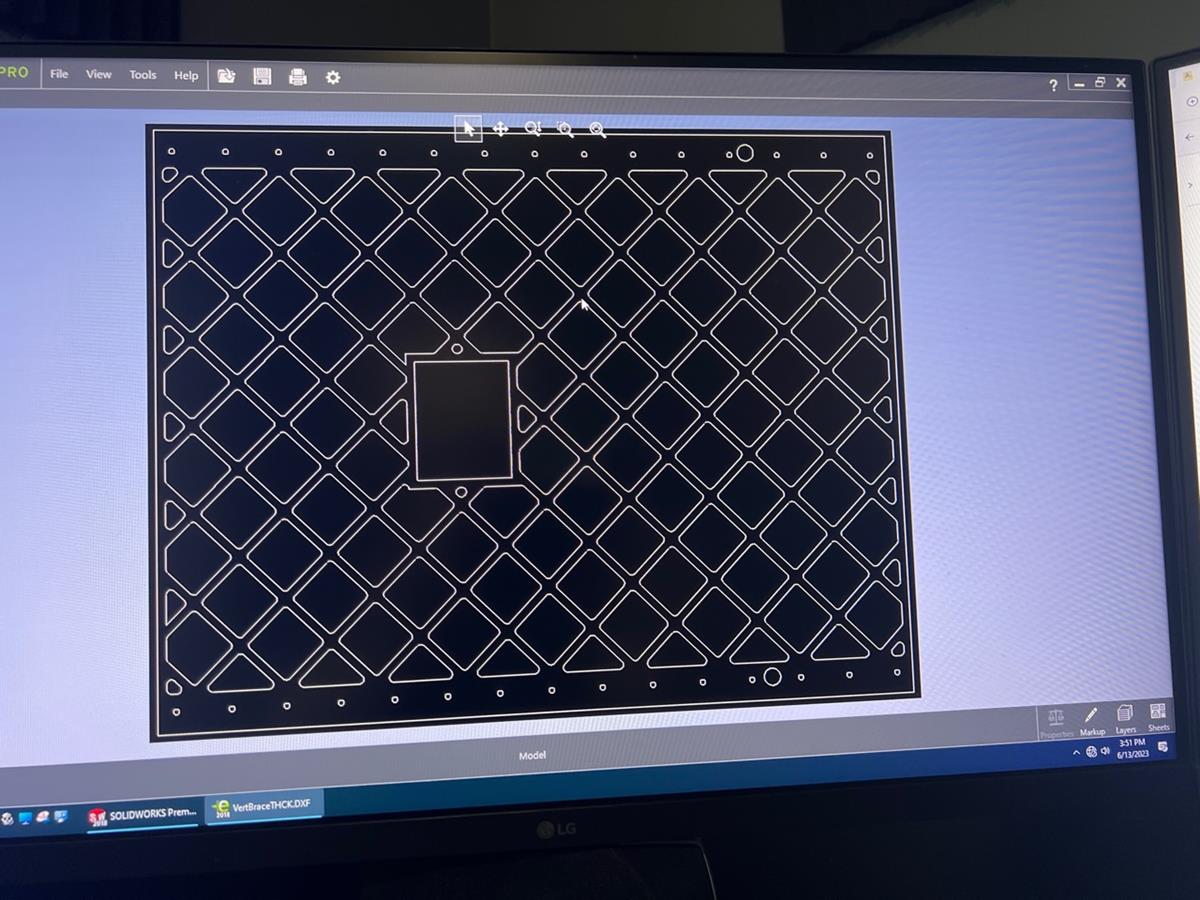
Part actually being cut 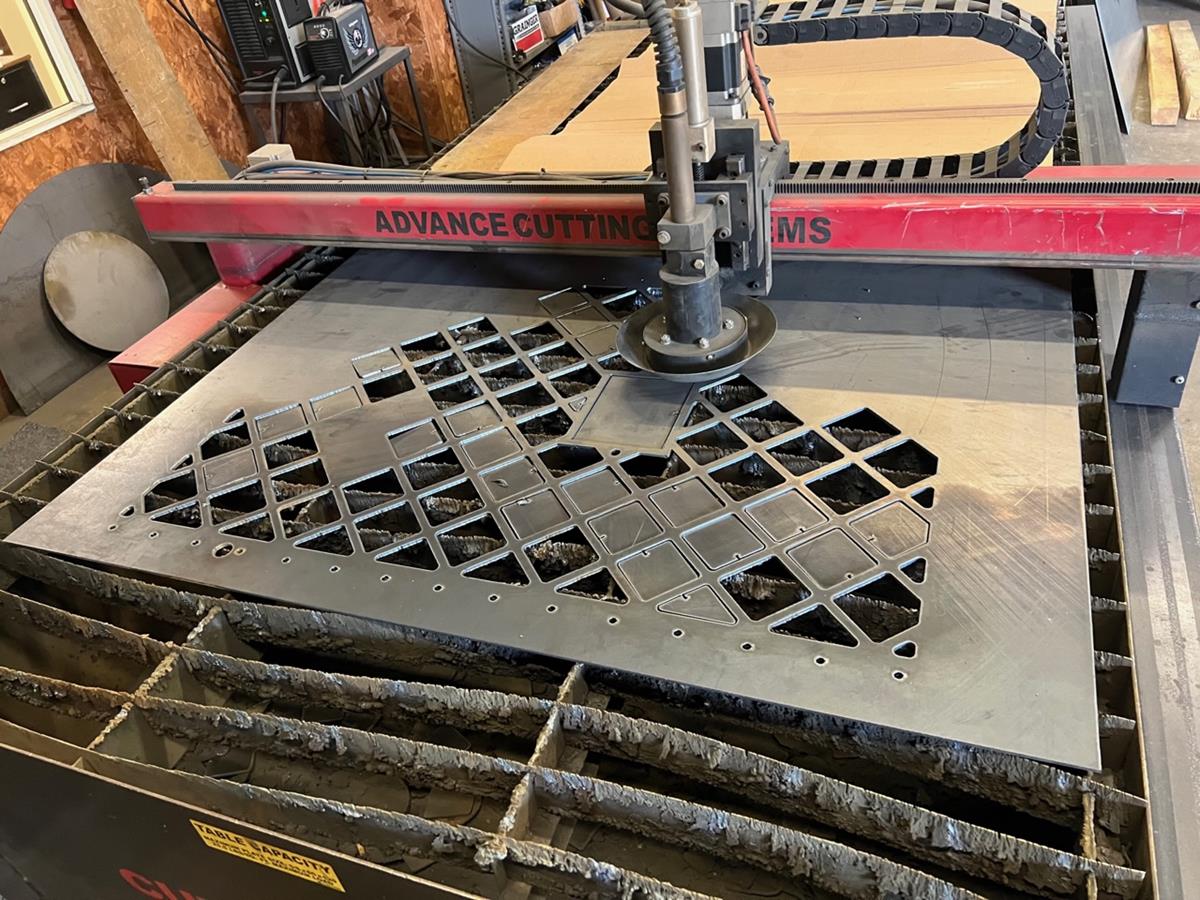
Test fit 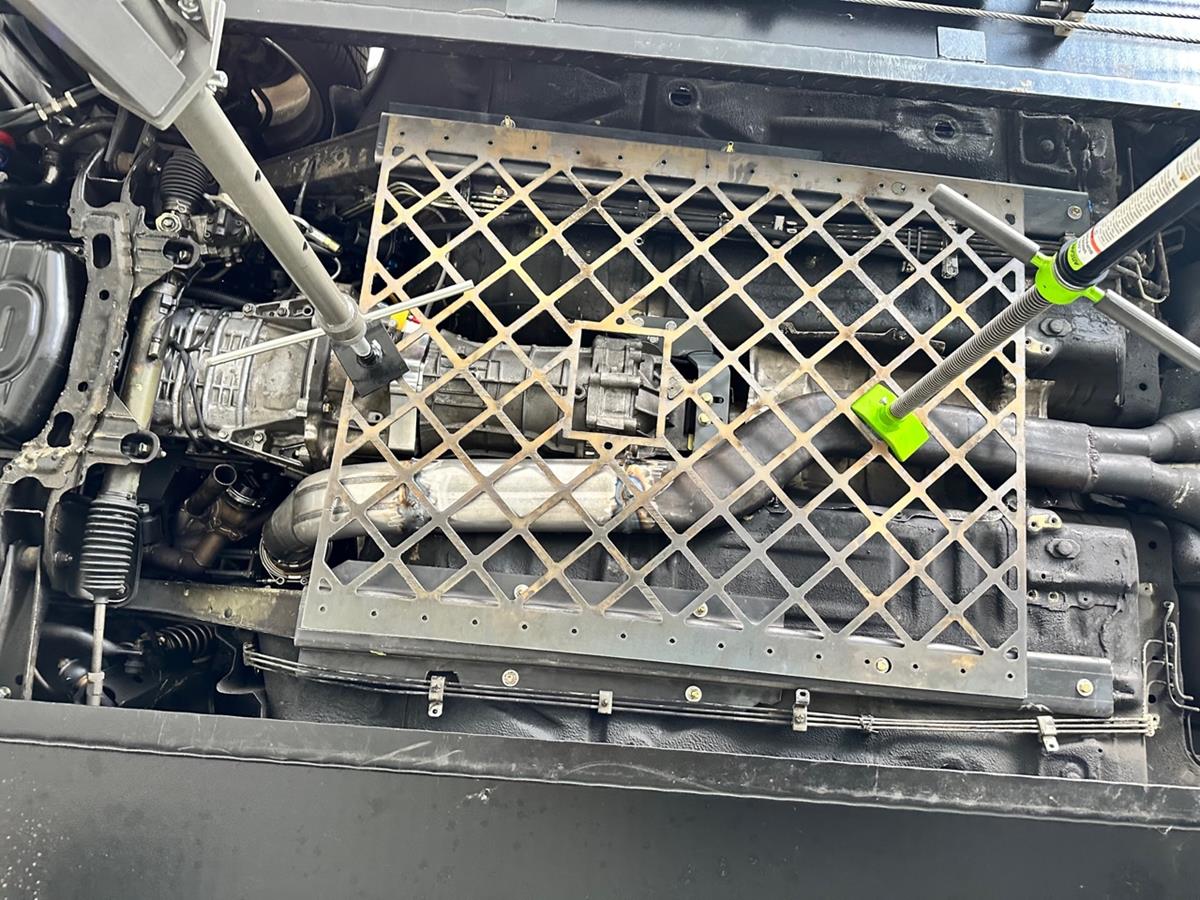
This part ultimately ended up being too thin to provide the support we wanted. I went ahead and shared this just for any other would-be inventors to see that failure is a very normal part of the process. I feel like social media has just become a success reel and no one ever shows their mistakes. So back to the drawing board. We decided at this point to make a more tube style bracing system to better connect the rails that we built. Attachment rails being made 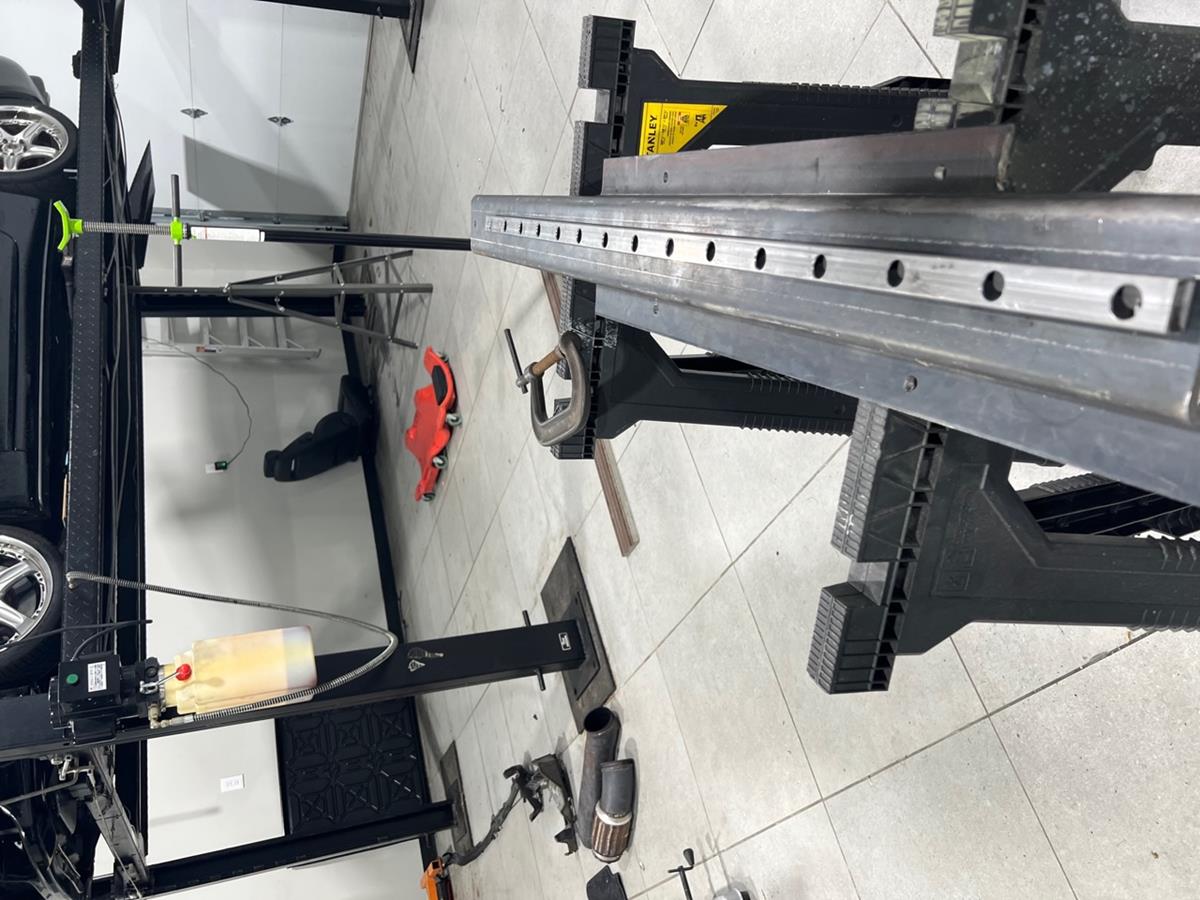
On the car mock up and starting to see what we had room for. 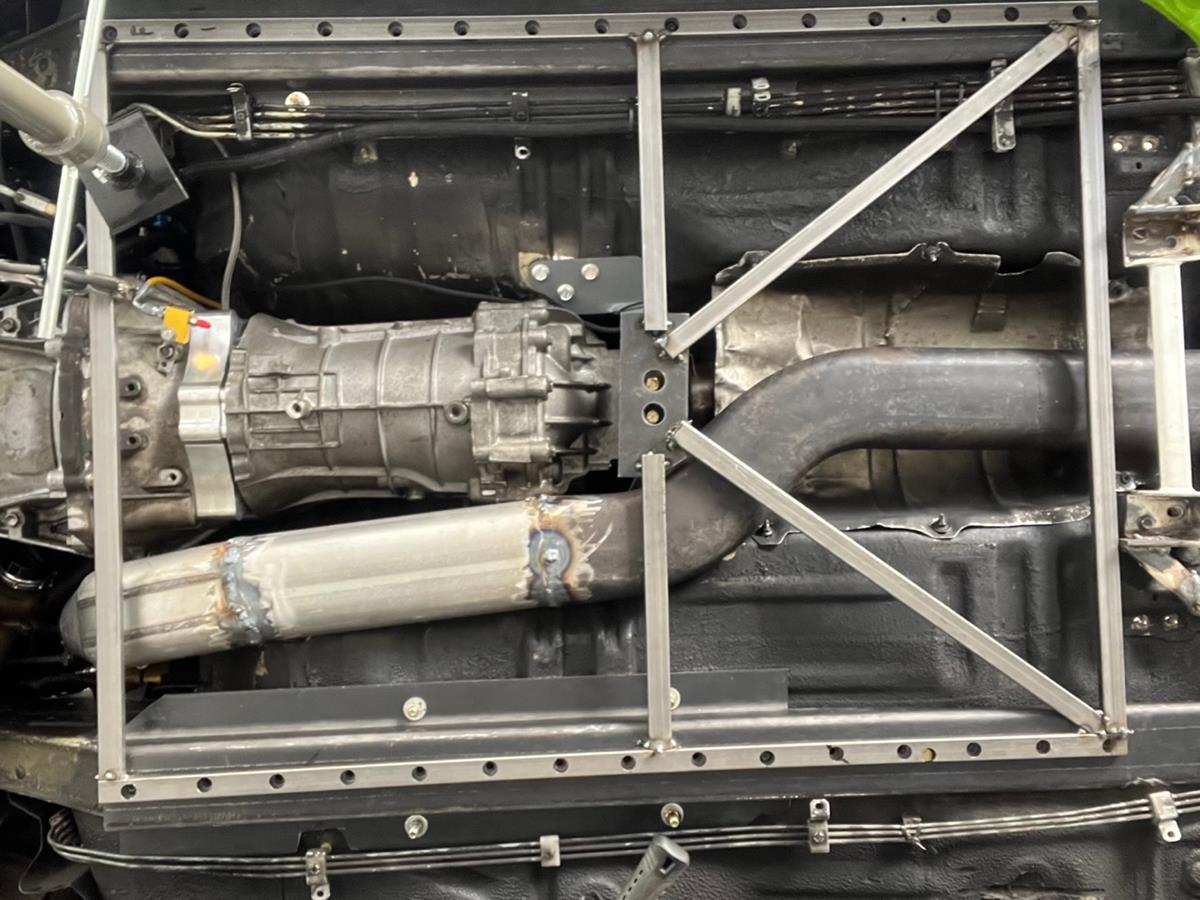
Our final product had a lot of asymmetry in it but to work around in the space we had available this was the best route we could see. 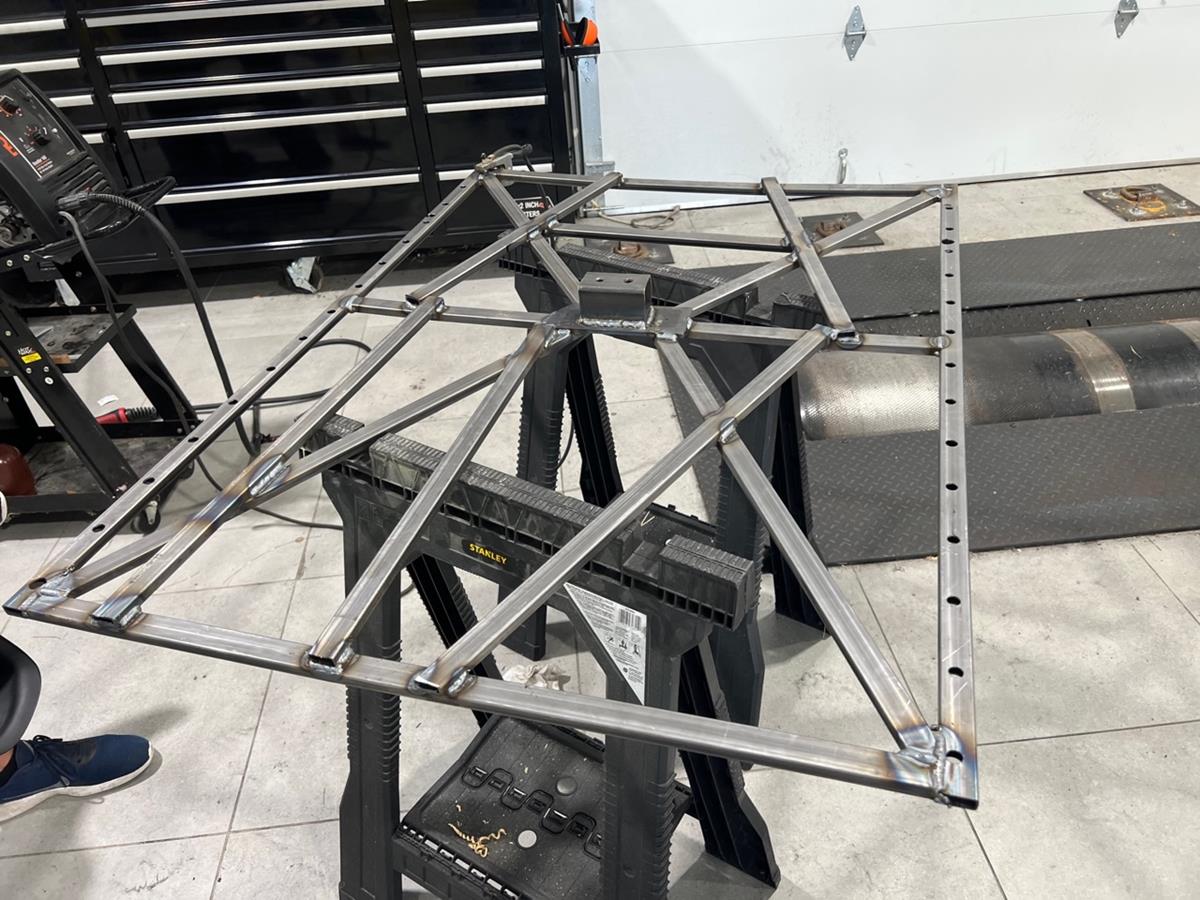
My MIG skills slowly improving (its odd I started with TIG and feel way more comfortable there) 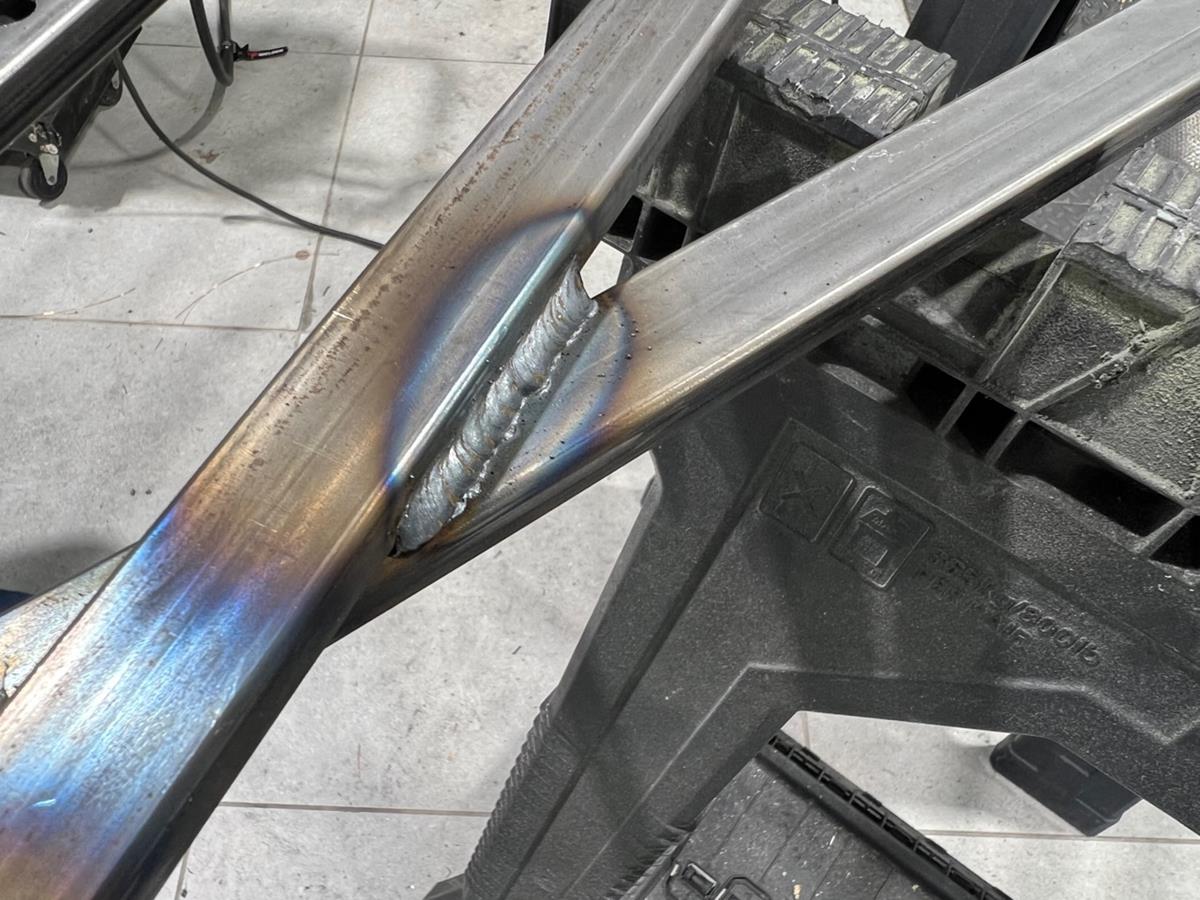
Everything getting painted 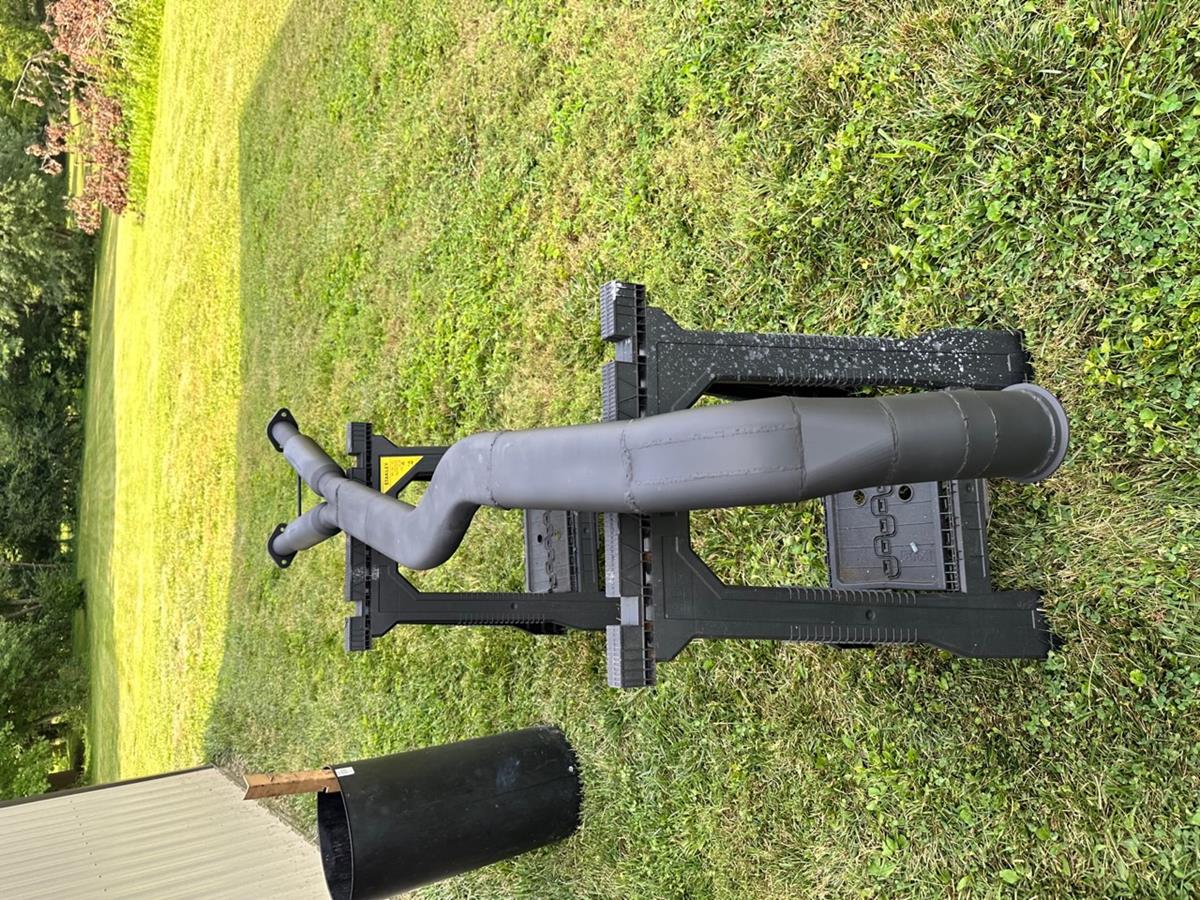
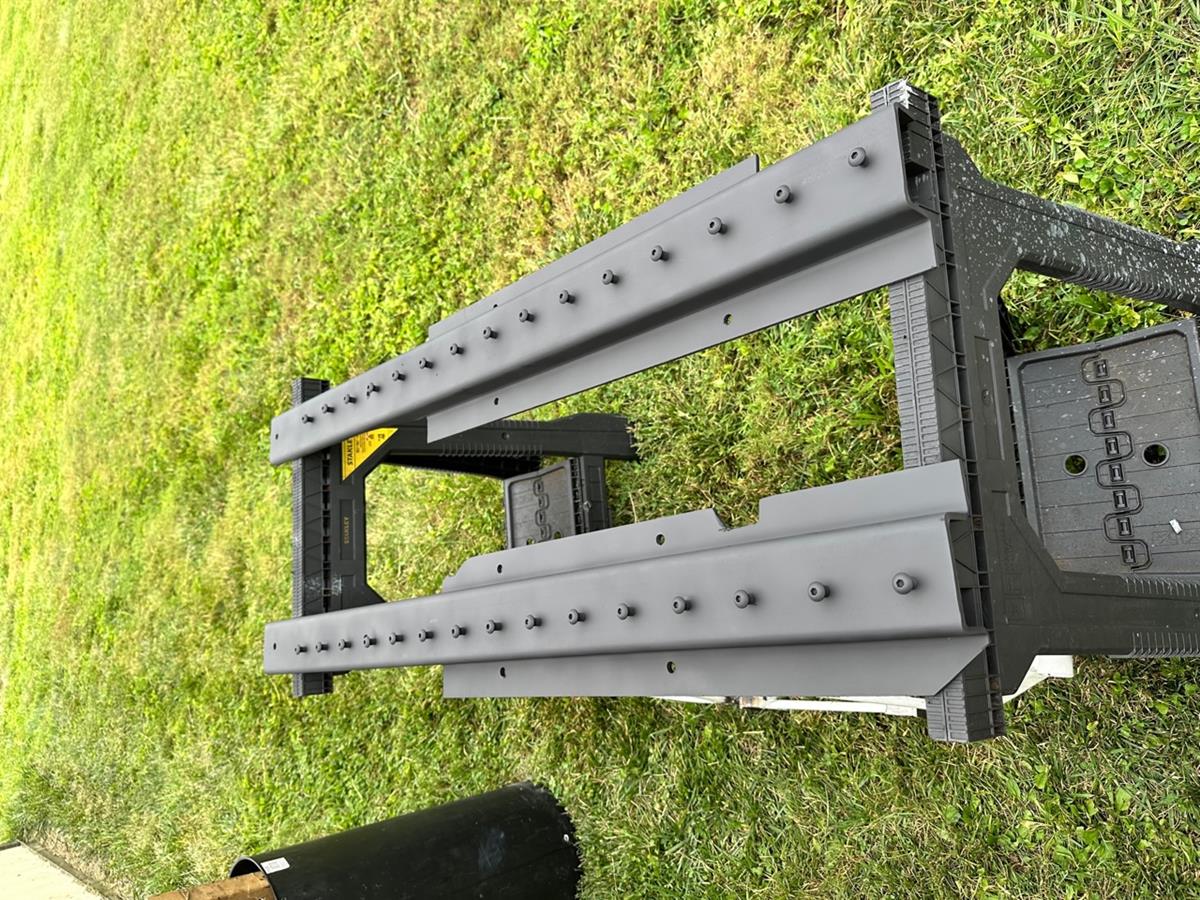
This was a part that another company made... It doesn't fit the Vert so we had to cut and weld on it to get it to work. 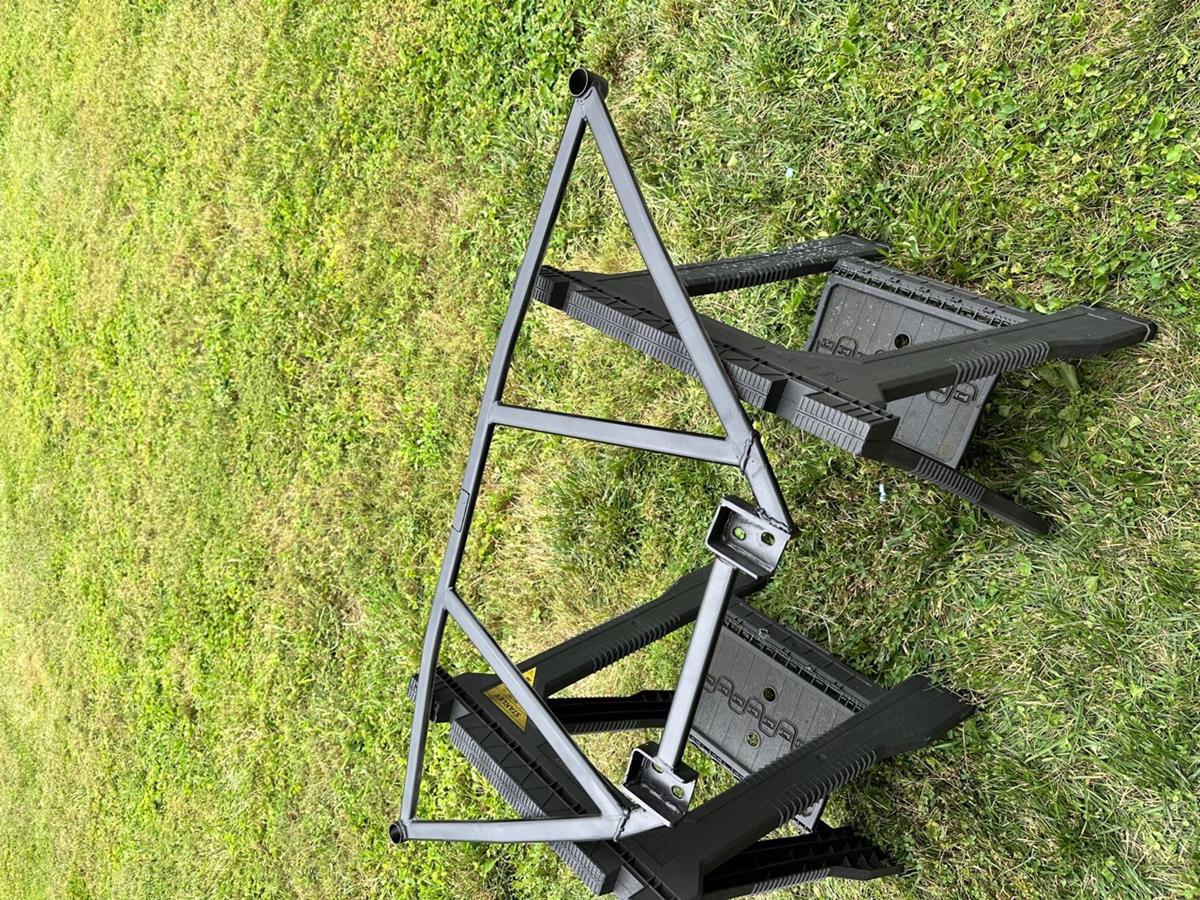
Brace all painted up 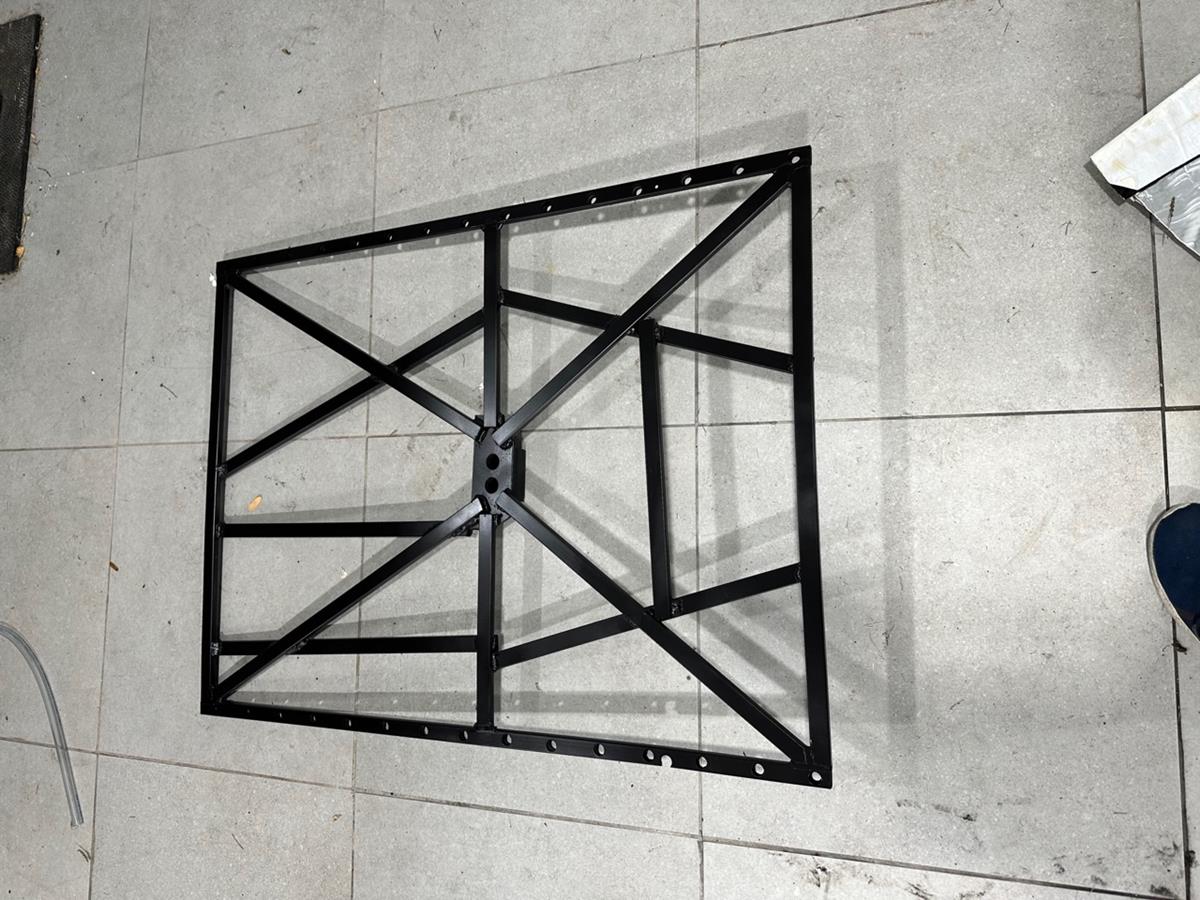
partially buttoned up 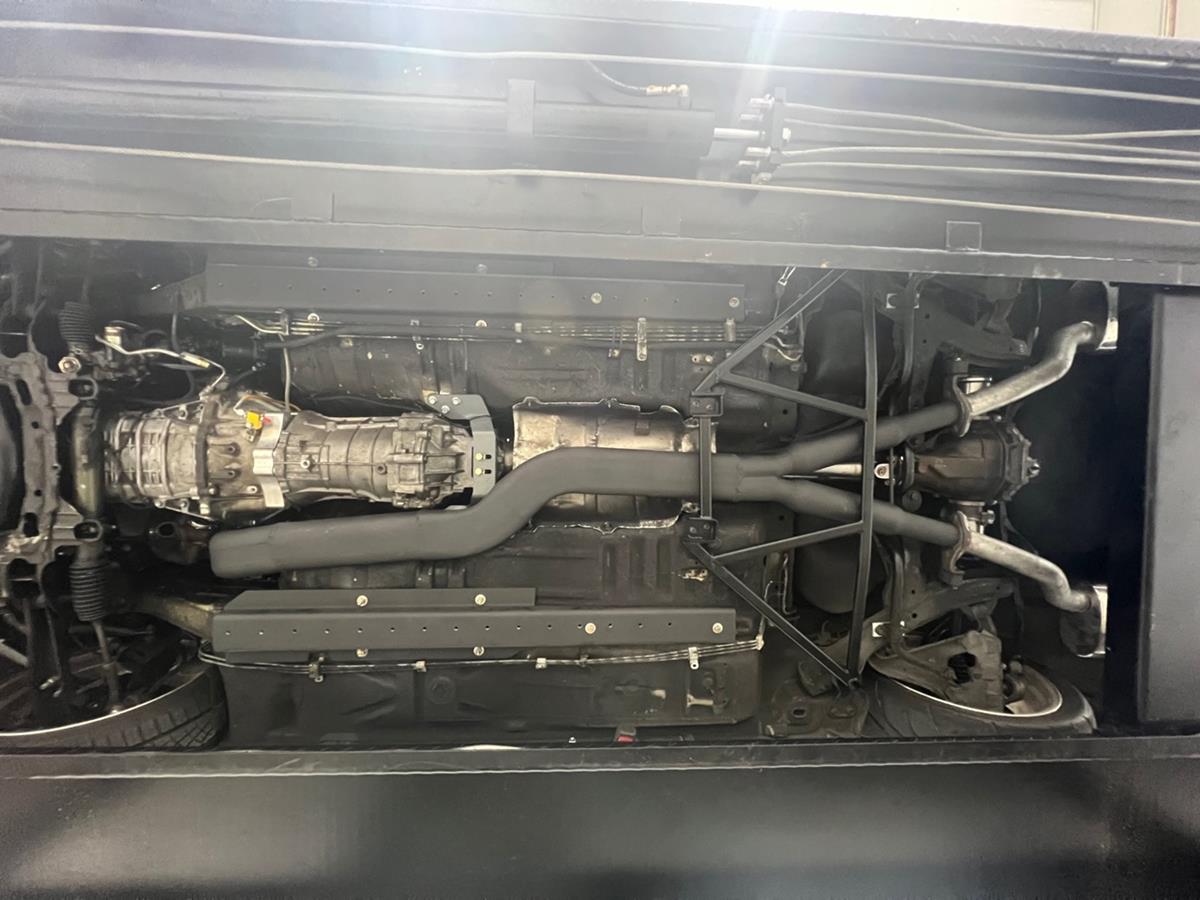
all done 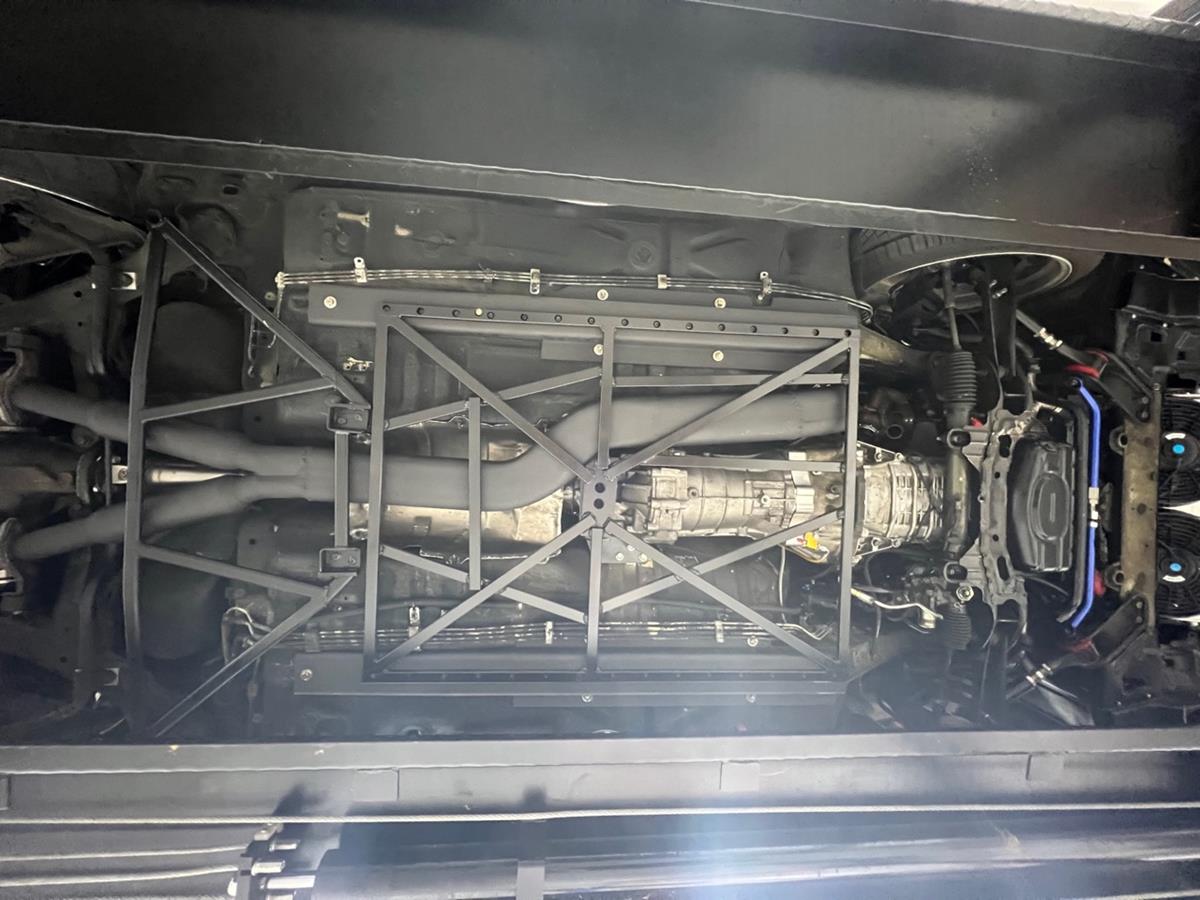
We did a lot of A/B testing with this project of driving the car with and without different components back to back. The bracing makes a substantial difference in the rigidity of the car and the overall quality of the driving experience. There is still an issue with his FUCAs we think causing a little bit of steering wheel feedback. But overall the project was a success.
Also, while the interior was out we started a refresh on some panels testing high end steam cleaners + Dye. The results are crazy.
Before on the left and after on the right. That's not a new panel....its how different we got it to look.
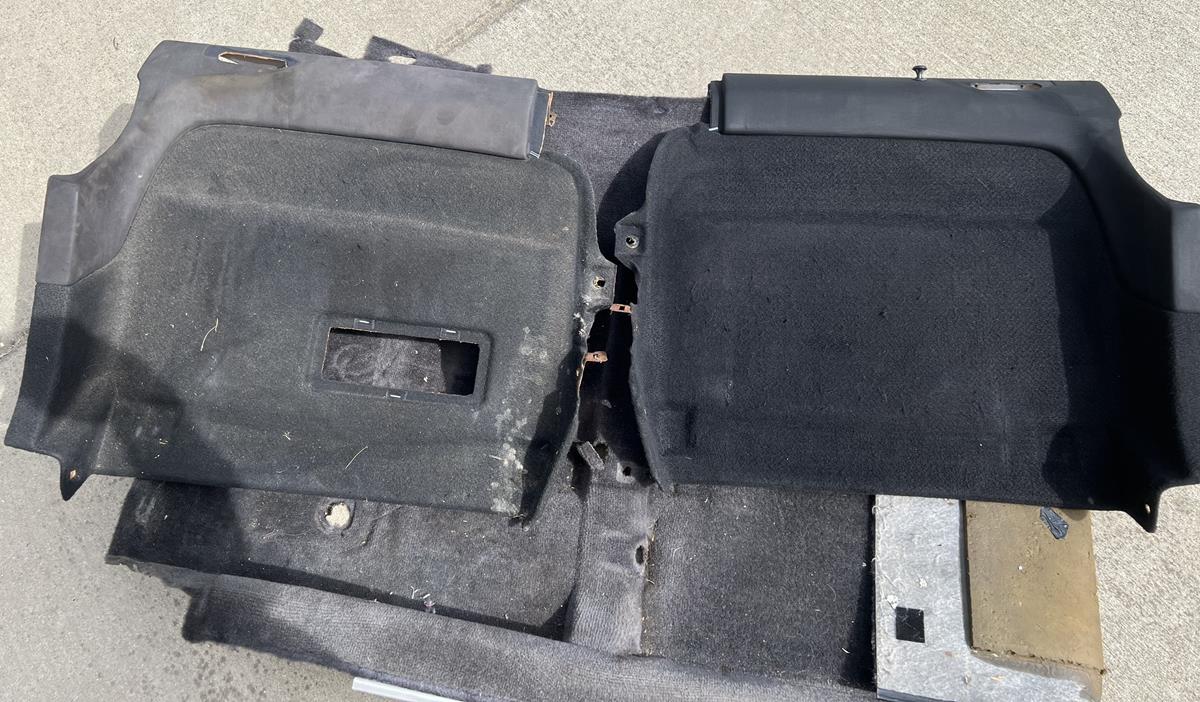
And some other pieces 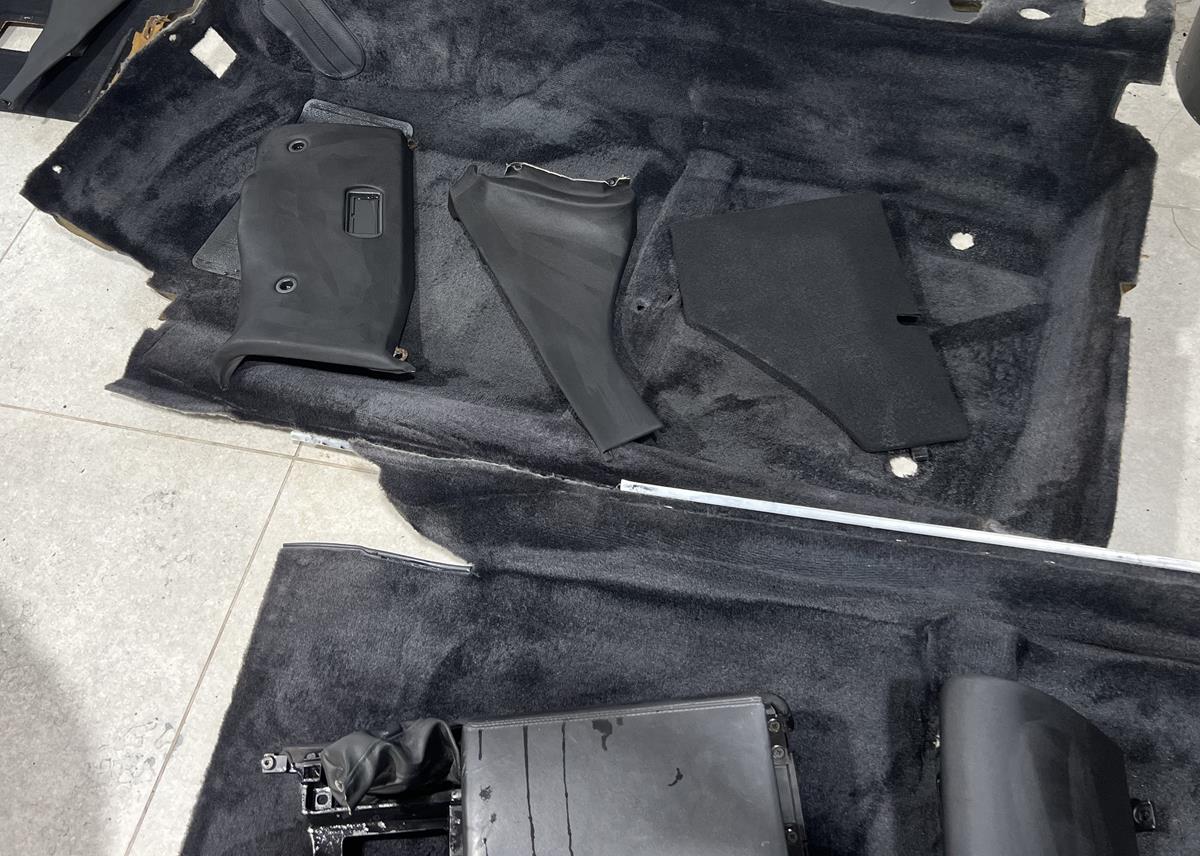
|